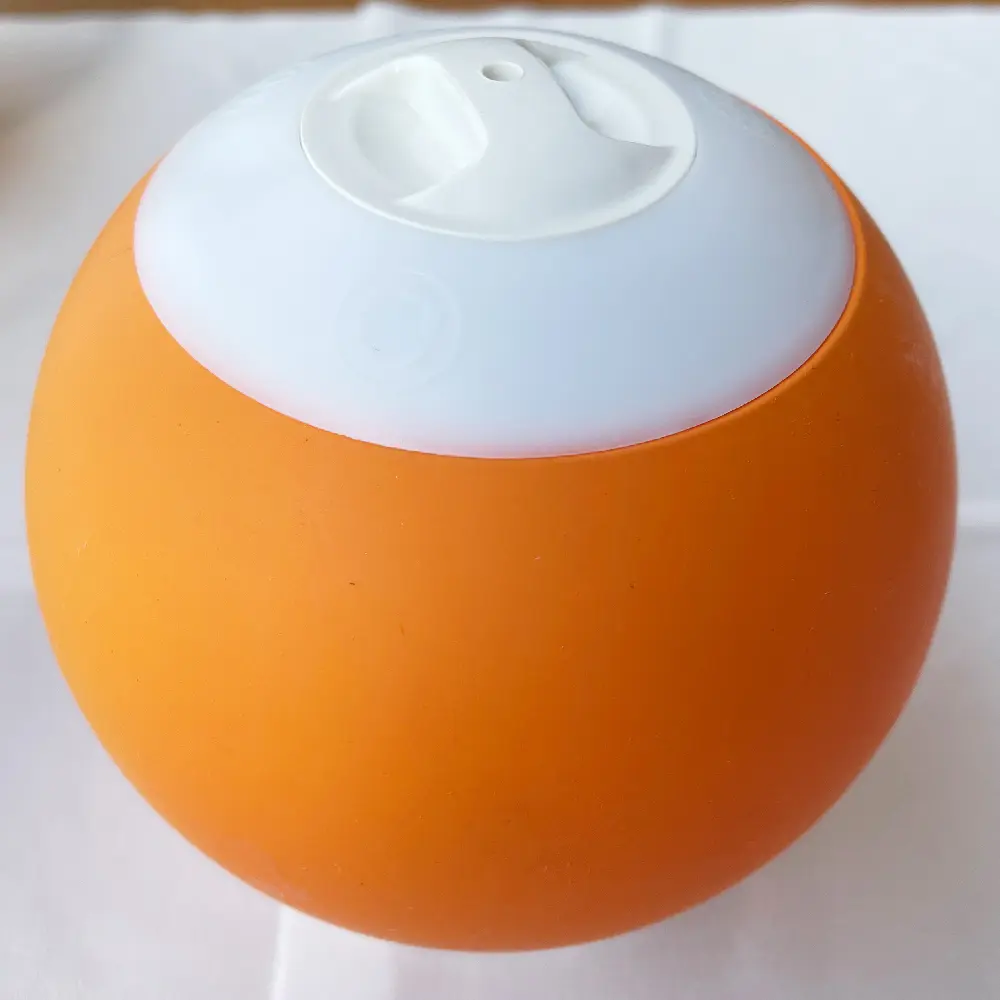
Low-volume Production for Housing with Vacuum Casting Process
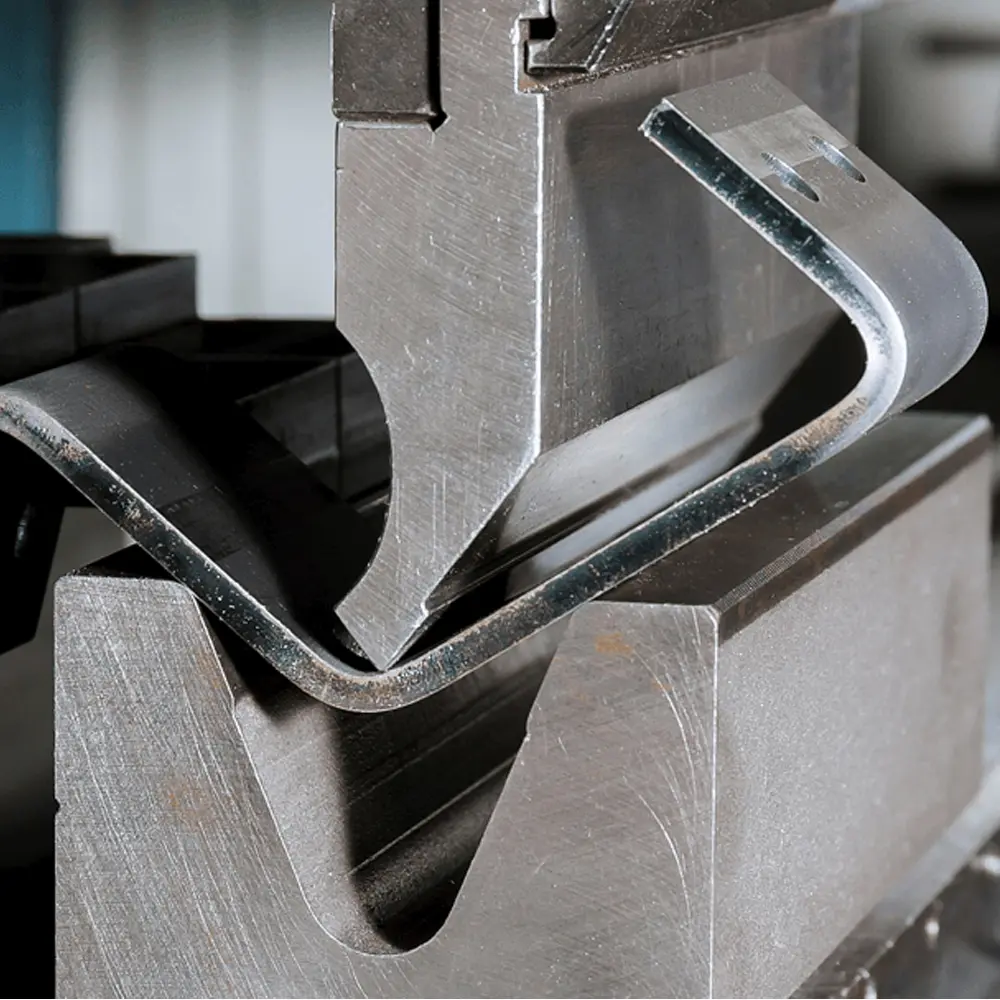
Design Tips to Sheet Metal
1. Hole Depths and Diameters
In product design, we always design some deep holes and small diameter holes. From manufacture side, we usually use CNC process to machine these features out. If the hole depth is smaller than 8 times of diameter, it can be normally and easily machined by CNC. If the hole depth is between 8 diameters and 10 diameters, the machining cost will be increased a little due to the risk of cutter break. However, If the hole depth is over than 10 diameters, we need to setup deep hole tools and process. This will increase cost obviously. If some deep hole features are must to your product design, please email us and we have some special CNC machining tips for you to save your cost. All these CNC machining tips are from our machining experience. We believe these CNC machining tips do help to product design.
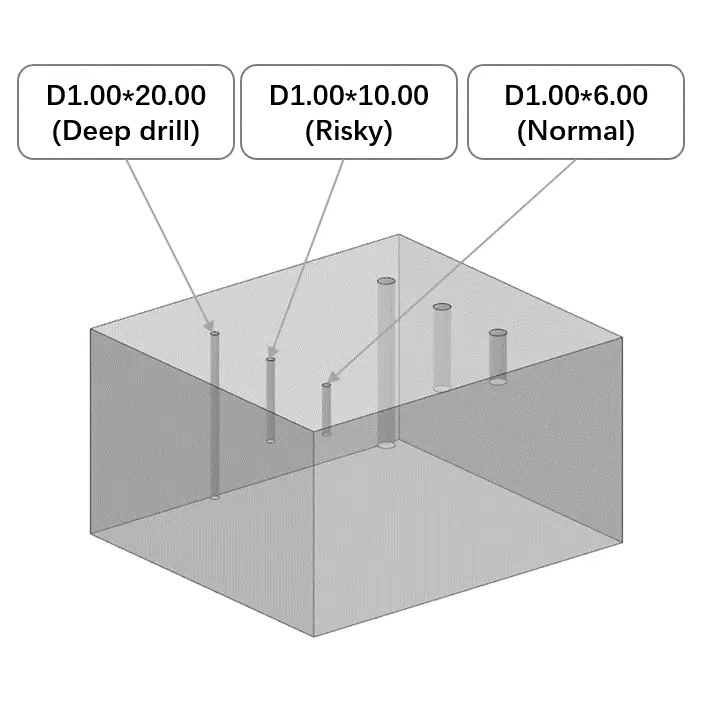
2. Wall Heights and Tiny Features
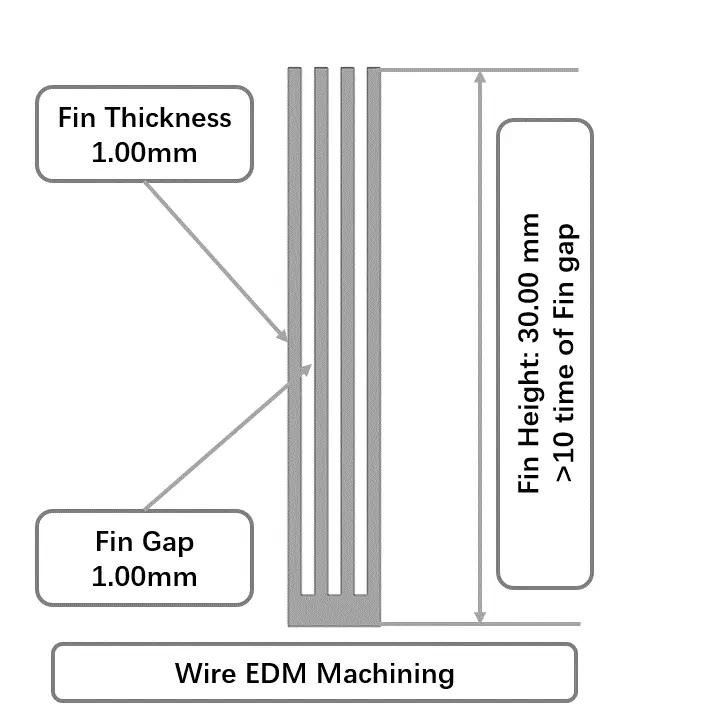
In product design, the wall height, thickness and tiny feature sizes are very dependent on the individual part geometry and the toolset being used. All of our toolsets are comprised of carbide cutting tools. This super rigid material offers maximum tool life and productivity with minimal deflection. However, we still provide you some CNC machining tips and hope these CNC machining tips can help you to save your product development cost. We strongly propose to design the wall height with thickness over than 0.5mm, the wall gap follow the strength of the cutters. If the wall gap is too narrow and deep, we need to use wire cut instead of CNC machining. The wire cut process will increase the cost. If possible, we propose to avoid super tiny features in your design. All these CNC machining tips here do help to save your product development cost.
3. Provide Relief to Corner Pockets
When you design a product, the pocket feature is, some time, a must for sitting some other parts in assembly. Mostly, we need to design a radius at 4 corners from manufacture side since we generally use CNC machining to cut out these pocket features. Here we have some CNC machining tips for you. If you can add radius to corners of pocket, please design is as large as you can. The larger cutter can cut out the radius in less CT. and smaller radius, sometimes, if the pocket is too deep, these radius can not be cut out by CNC machining, in this case, the cost will increased since we need to use spark EDM. If the sharp corners are must, we have to use spark EDM and this process will increase the machining cost of your design. All these CNC machining tips here are for your to make your design machinable and be in lower cost.
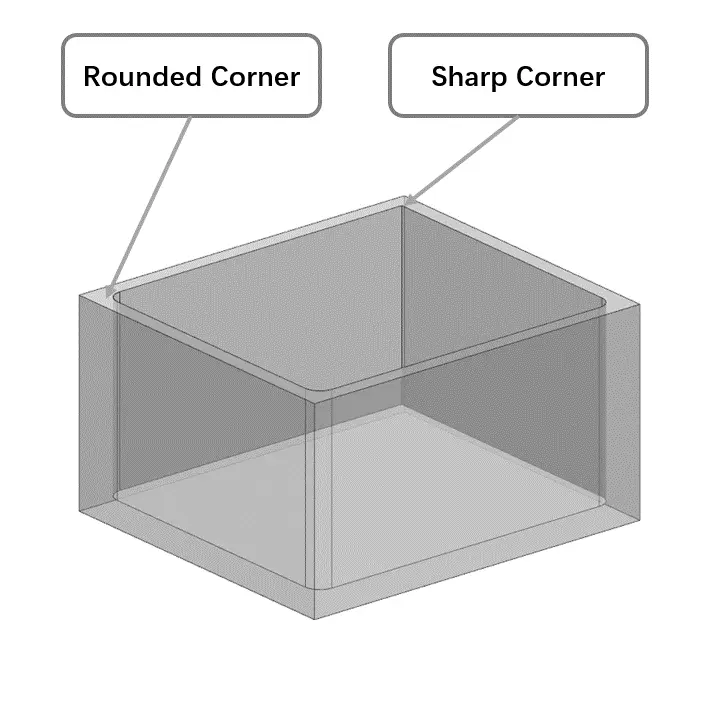
4. Interlock features
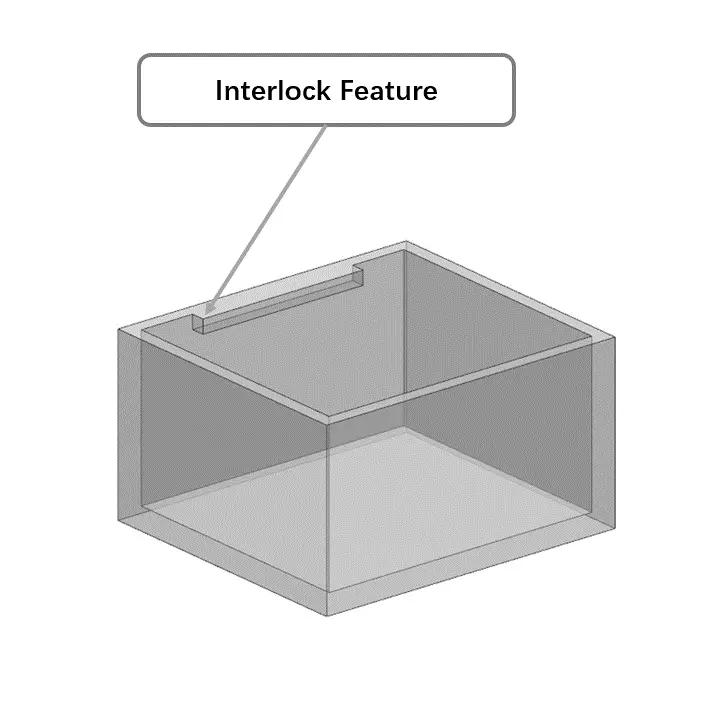
When you design an interlock feature onto product, please take T cutter limitation into your consideration. Here we have CNC machining tips to interlock features, if the CNC machining can cut out all the interlock feature you designed with T cutters, that will be good design. If not, we need to take some other action to machine it, such as 5 axis CNC, spark EDM, etc. In order to save machining cost, we use 5 axis CNC machining when necessary. And we always use DFM to propose customers to remove EDM features from their design since these features are costly. We also have special CNC machining tips if the customer insists on designing a unmachinable interlock feature. One is to machine the interlock fearures individually and then assembly it onto the main body by screwing or welding. If you want to learn more CNC machining tips, please visit our Facebook page and YouTube Channel.