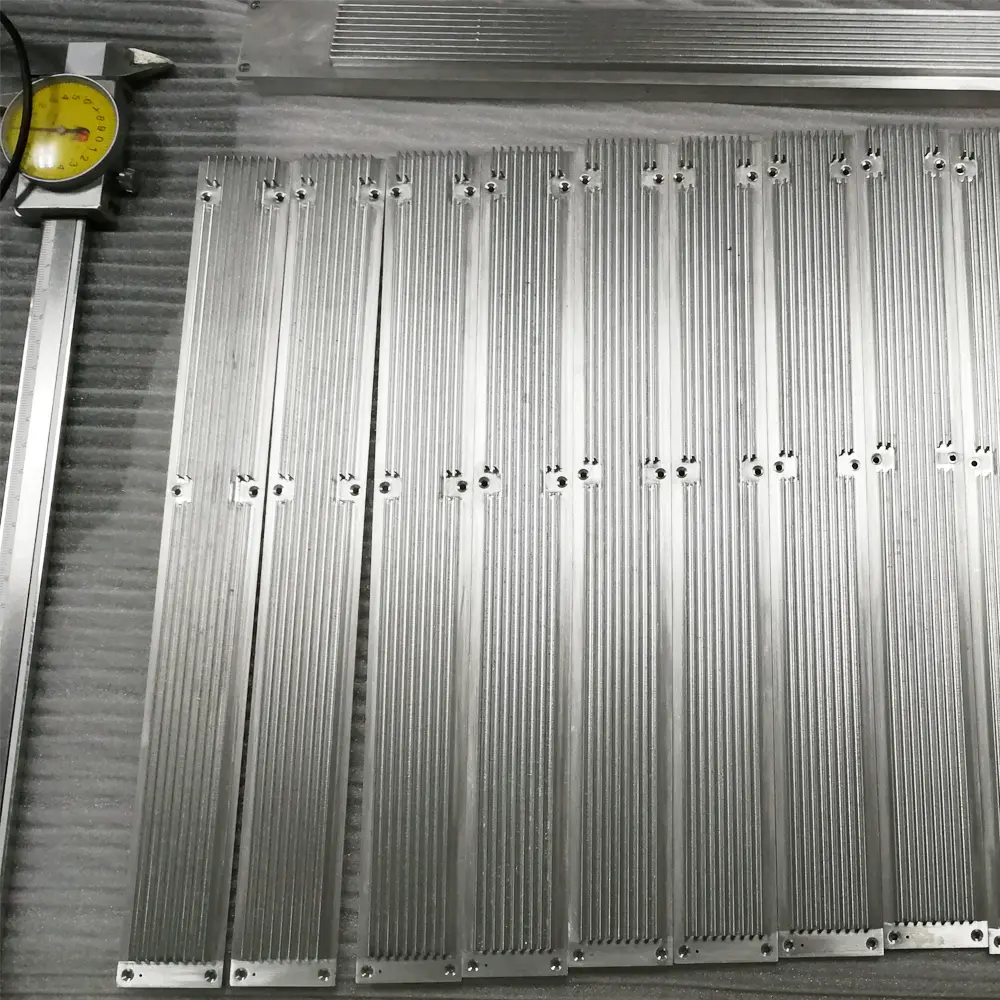
Anodized Aluminum Enclosure with Specified Region Keeping Free from Anodization
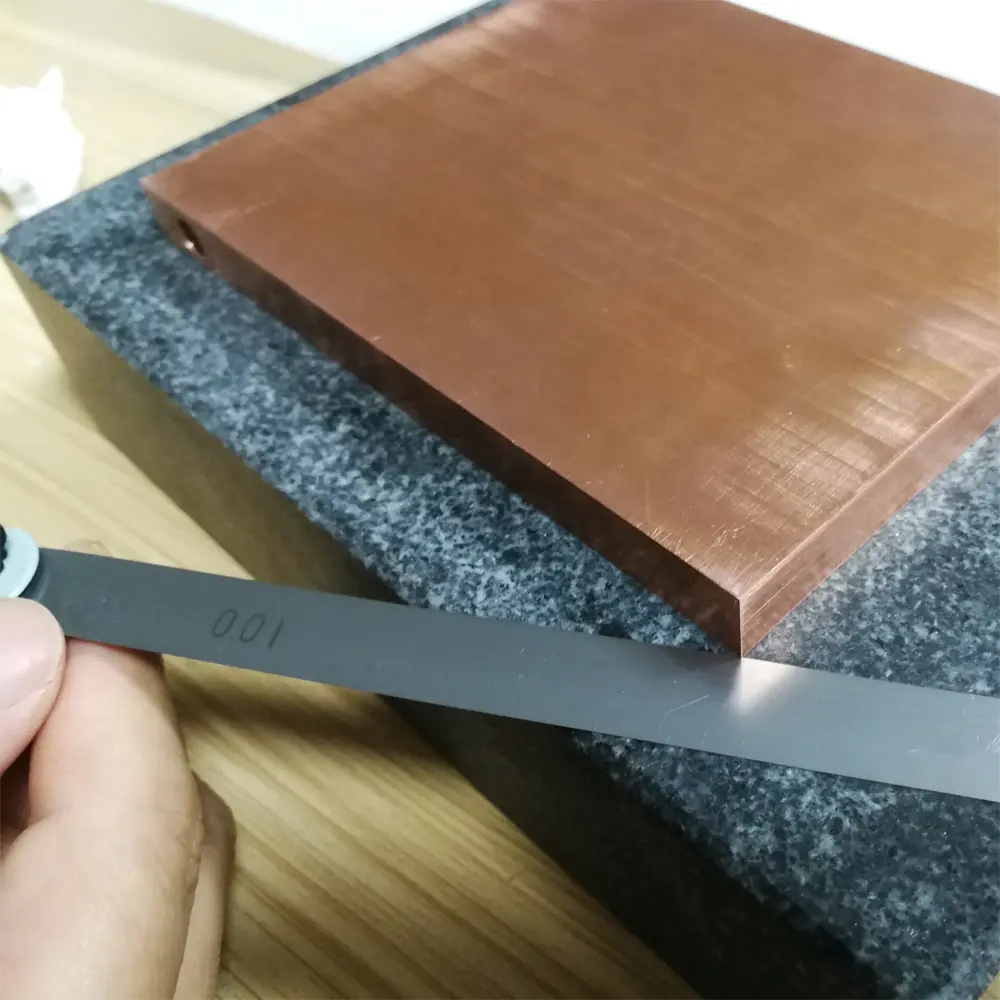
Copper Covers with Machined by CNC Machining and Grinding Processing for Back Surface Because Its Flatness Tolerance of 0.01mm
Low Volume Production for a Multi-Camera Aluminum Housing with CNC Machining Techniques
Manufacturing Services: CNC Machining, Anodization, Vacuum Casting, 3D Printing, Assembly.
Finishing Services: Anodizing, Painting
Material Used: Aluminum, ABS, Silicone
Prototype Type: CNC machining techniques prototype
Challenge: Using 3 axis CNC to machine complex features
Prototyping Quantity: 50 sets
Lead Time: 20 days
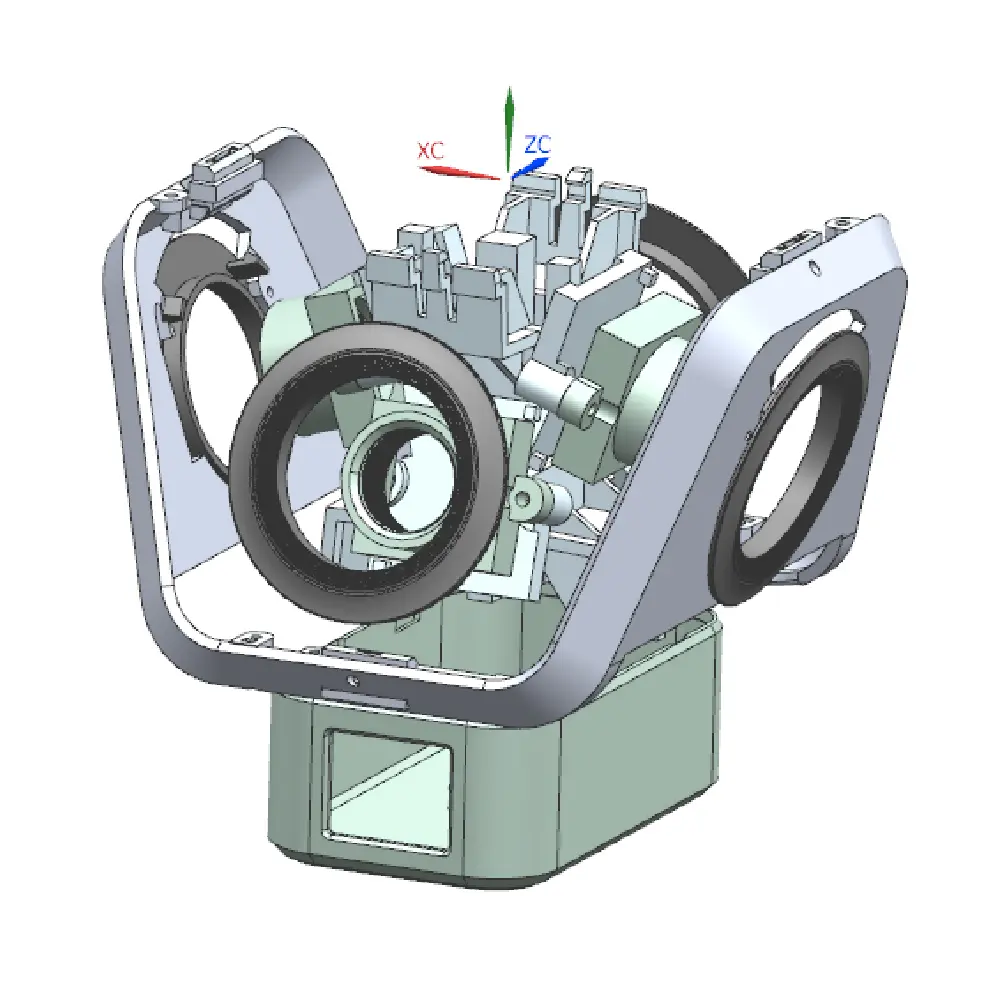
About the CNC Machining Techniques Prototype
This is a low-volume production project, the customer needs these parts for their first step market. And they will need more according to the result of prototype samples. The date for announcing this product to market is fixed. So, samples’ manufacturing must follow the schedule. Additionally, these parts will meet the end users, so the samples must be in a high dimension accuracy and good cosmetic. The customer is working on business with camera products. Both dimension precision and finishing are required much.
The is a small product but with many internal parts installed in. We need to manufacture all the internal parts and assembly them together. Some parts are designed to move while some inside is designed in very complex geometry. And the main process for this project is CNC machining techniques. By the way, the housing is required to do anodizing and must be in good finishing. The CNC machining for this rotating camera housing should be in high precision since the tolerance control in very narrow range in customers’ 2D drawing. Also, the machining cost must be much lower than prototypes since these 50 sets will be shipped to its first end users.
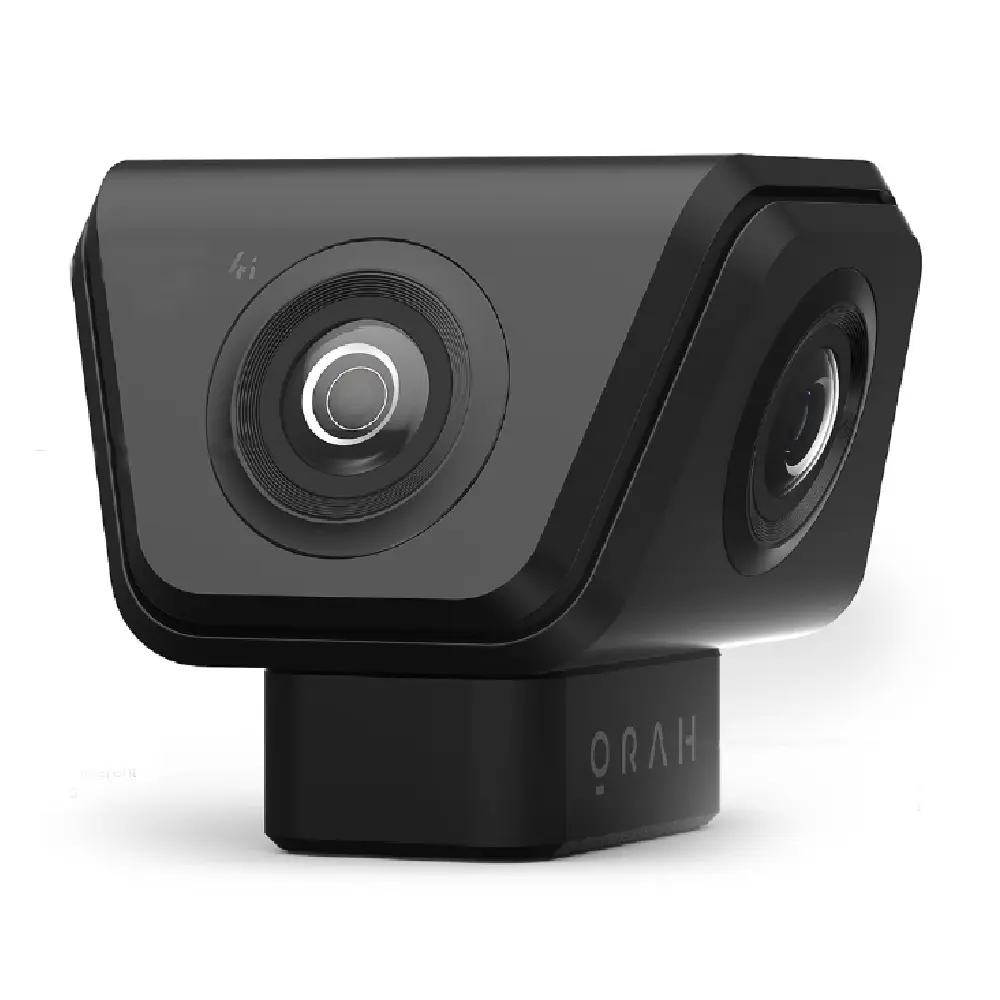
Challenges in the CNC Machining Techniques Prototype
This project is a great challenge for CNC machining. Some internal parts are really too complex to machine by 3 axes CNC. We tried to machine it with 5 axes CNC, but it still didn’t work since some internal features still can’t machine out. After a negotiation with customer, we are allowed to use 3D printing and manual relief processes to manufacture the complex internal parts instead of CNC machining techniques. The precision of aluminum housing and camera rings is another challenge, they have to be assembled in small and insistent gaps. We adopted sorting after CNC machining, which is machining many extra camera rings and then do hand fit and inspecting to sort the right one. Finally, after a hard work, we finished all these 50 sets and made customers satisfied.
From this project, we learnt that CNC machining techniques can do many precision parts, but it still has many complex features can’t be machined out. In this case, we should not use CNC machining techniques only, we should try to machine a similar geometry with the design and then use some other post process like relieving, polishing, grinding to achieve the final geometry. For more cases, you can review on our Facebook page or YouTube channel.
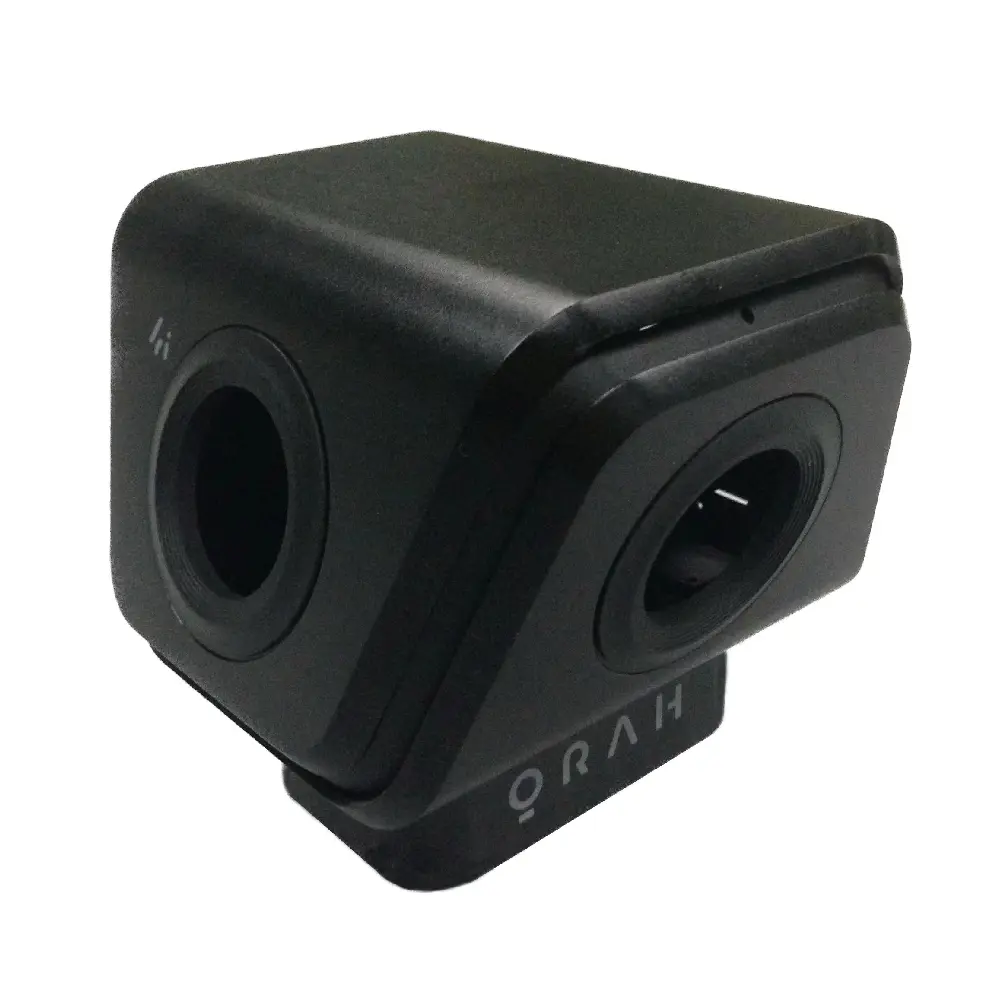