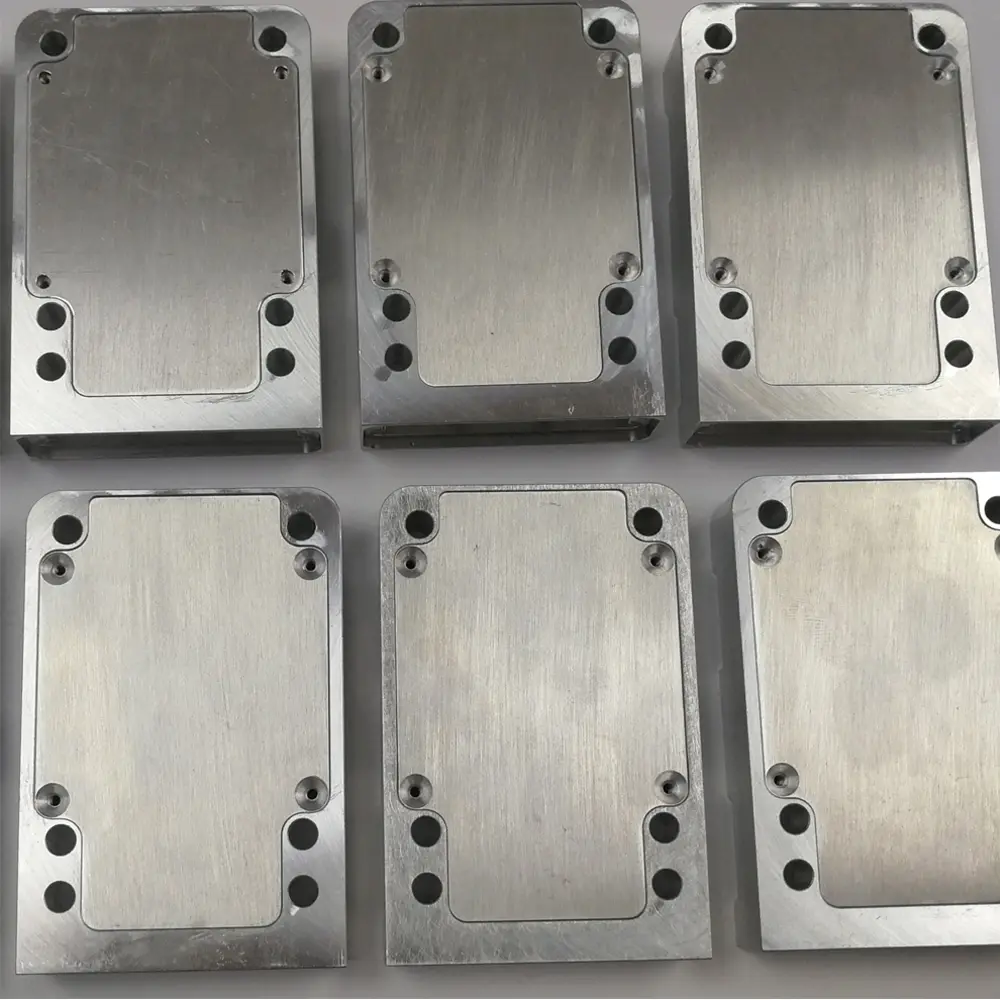
Low Volume Production with Manufacturing Process for Aluminum Housing and Lid
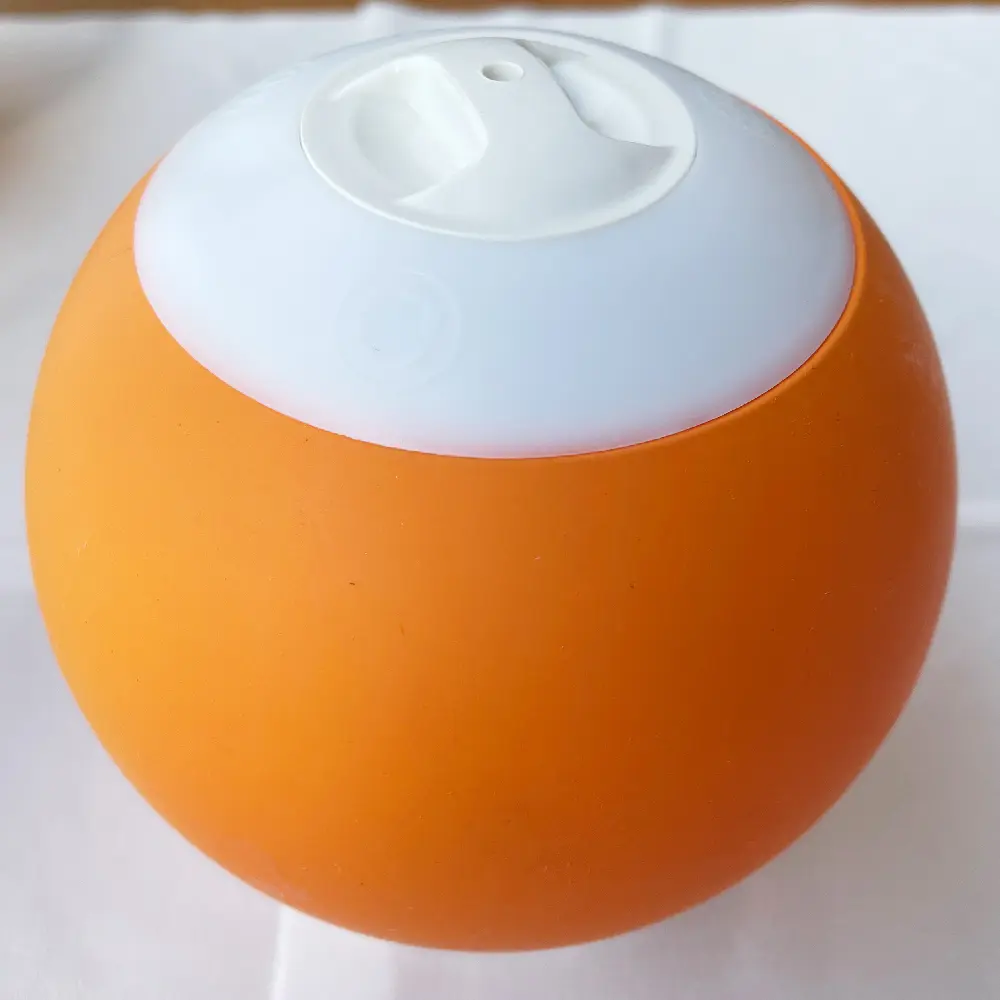
Low-volume Production for Housing with Vacuum Casting Process
Liquid Silicone Rubber Prototyping for Press Button of Medica Devices
Manufacturing Services: Vacuum Casting
Finishing Services: Transparent
Material Used: Liquid Silicone Rubber
Prototype Type: Liquid silicone rubber prototyping
Challenge: Keeping section thickness consistent and transparence over than 90%
Prototyping Quantity: 300 sets
Lead Time: 30 days
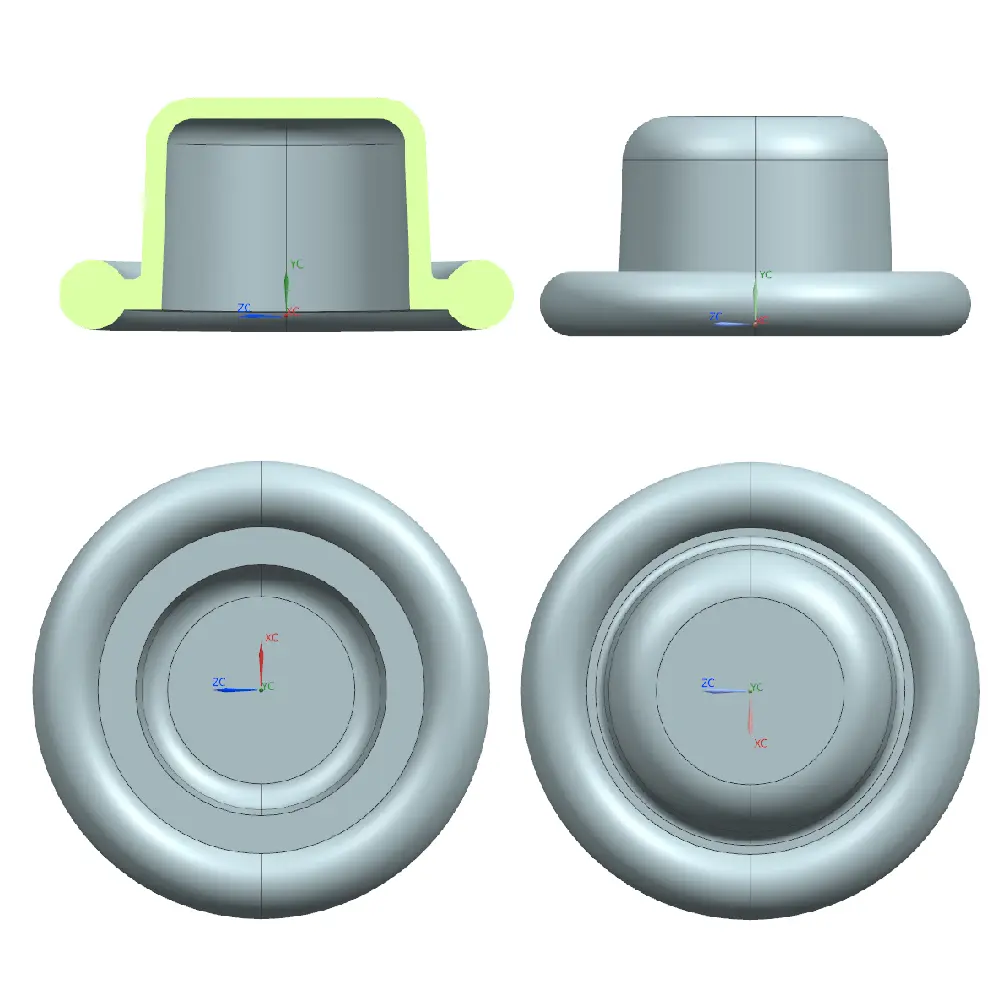
About the Liquid Silicone Rubber Prototyping
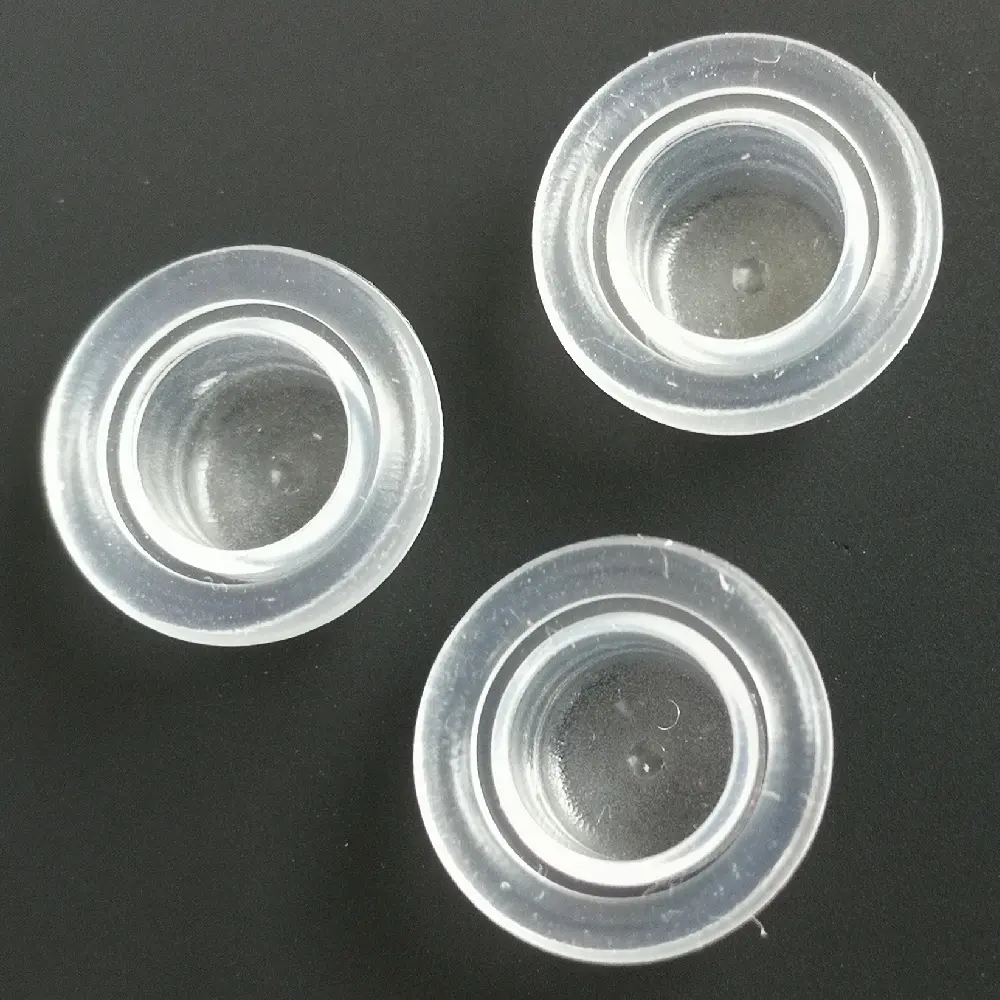
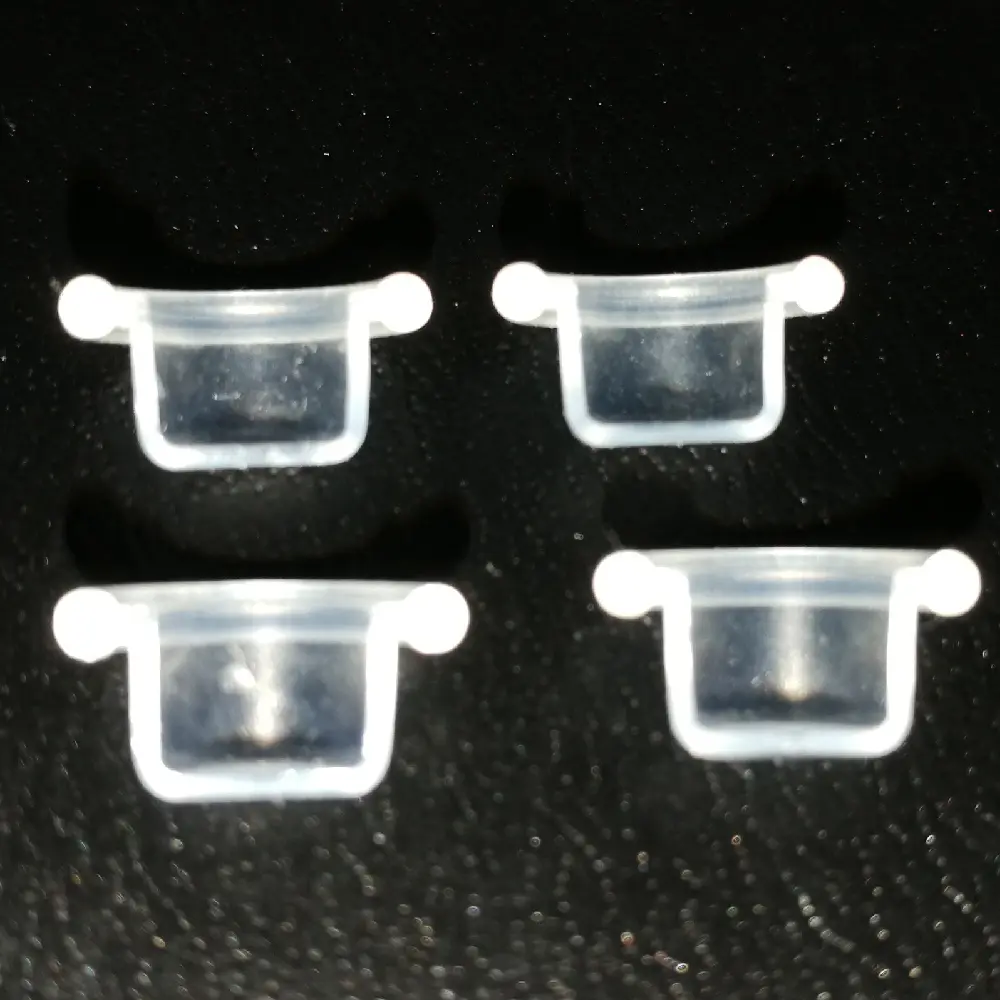
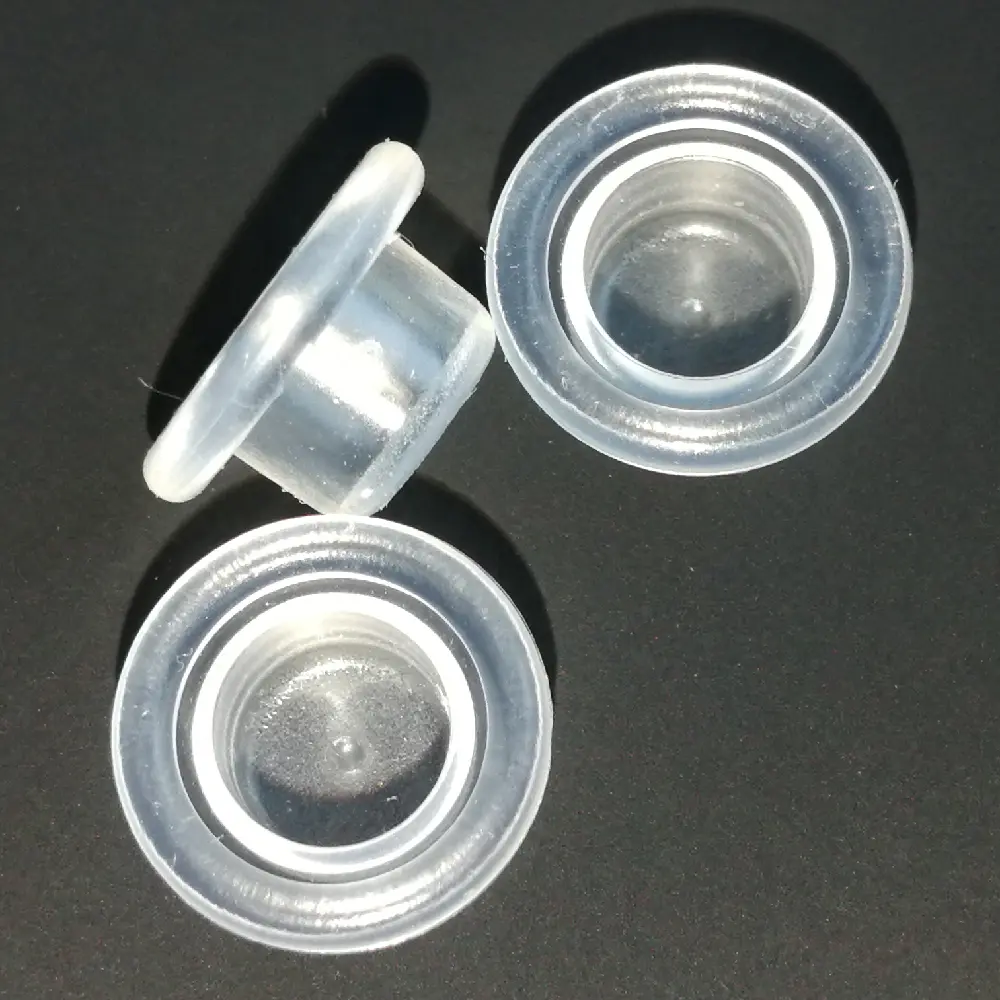
The parts in this liquid silicone rubber prototyping will be used as press button of medical devices. The customer specified material WACKER ELASTOSIL3003/50A to their products. We decided to use vacuum casting process for making these buttons due to its quantity of 300pcs. The best way to make high quality of these samples is kicking off liquid silicone mold and doing injection molding. However, the quantity of this project is only 300pcs and the cost of liquid silicone mold is too high. The customer would kick off liquid silicone mold after prototyping build since it still has high risk to make design change. Additionally, the customer needed these products in consistent thickness and transparent over than 90%. For vacuum casting process, it is difficult to ensure the thickness of parts with such liquid material due to its low hardness. But this time, we would have a try.
Challenges in Liquid Silicone Rubber Prototyping
For liquid silicone rubber product, it is difficult to control the dimension tolerance into +/-0.10mm. So, to kick off liquid silicone mold is a good way to ensure all the dimensions. For vacuum casting process, the general dimension tolerance is +/-0.10mm ~ +/-0.15mm. And for soft or lower hardness material the dimensions accuracy will get worse obviously. That means we need to do some work to improve the dimension accuracy.
For liquid silicone rubber samples, over 90% transparent is not a easy work, we also need to make our workshop in lower dust level. At OrideTech, the guys always like to challenge themselves. They set up a special room in low dust level just for this project to improve the transparent of these parts and also tried to increase the hardness of mold to improve the dimension precision. After all the actions, they confirmed all the details of material and process conditions, especially curing temperature and time to ensure that the samples are processing successfully. For more cases, you can review on our Facebook page or YouTube channel.
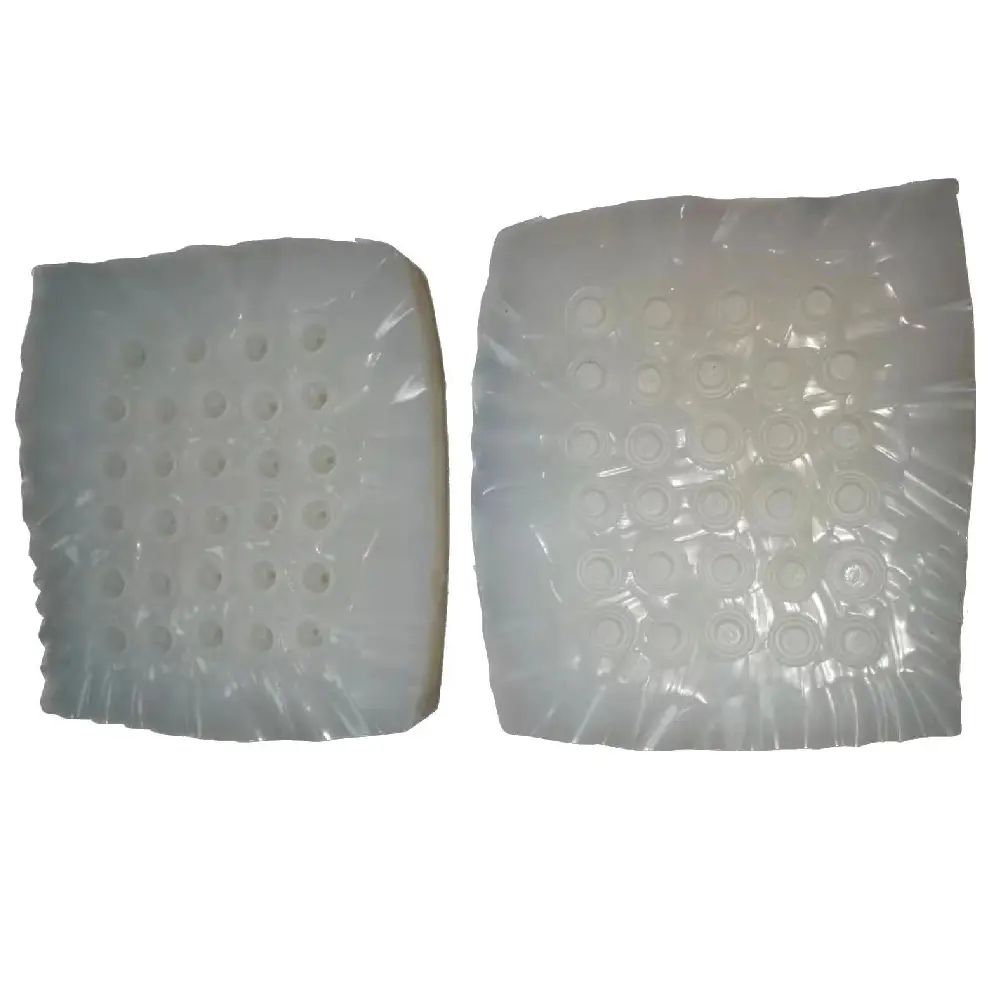