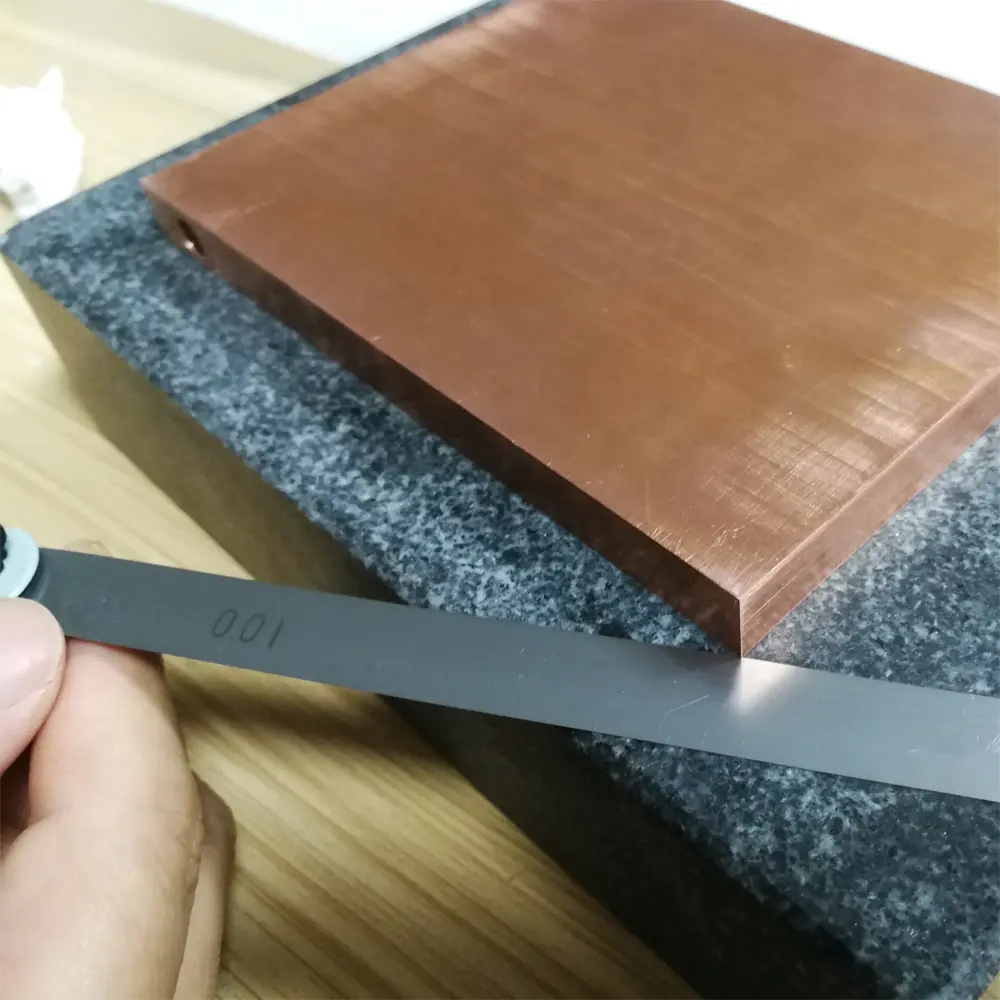
Copper Covers with Machined by CNC Machining and Grinding Processing for Back Surface Because Its Flatness Tolerance of 0.01mm
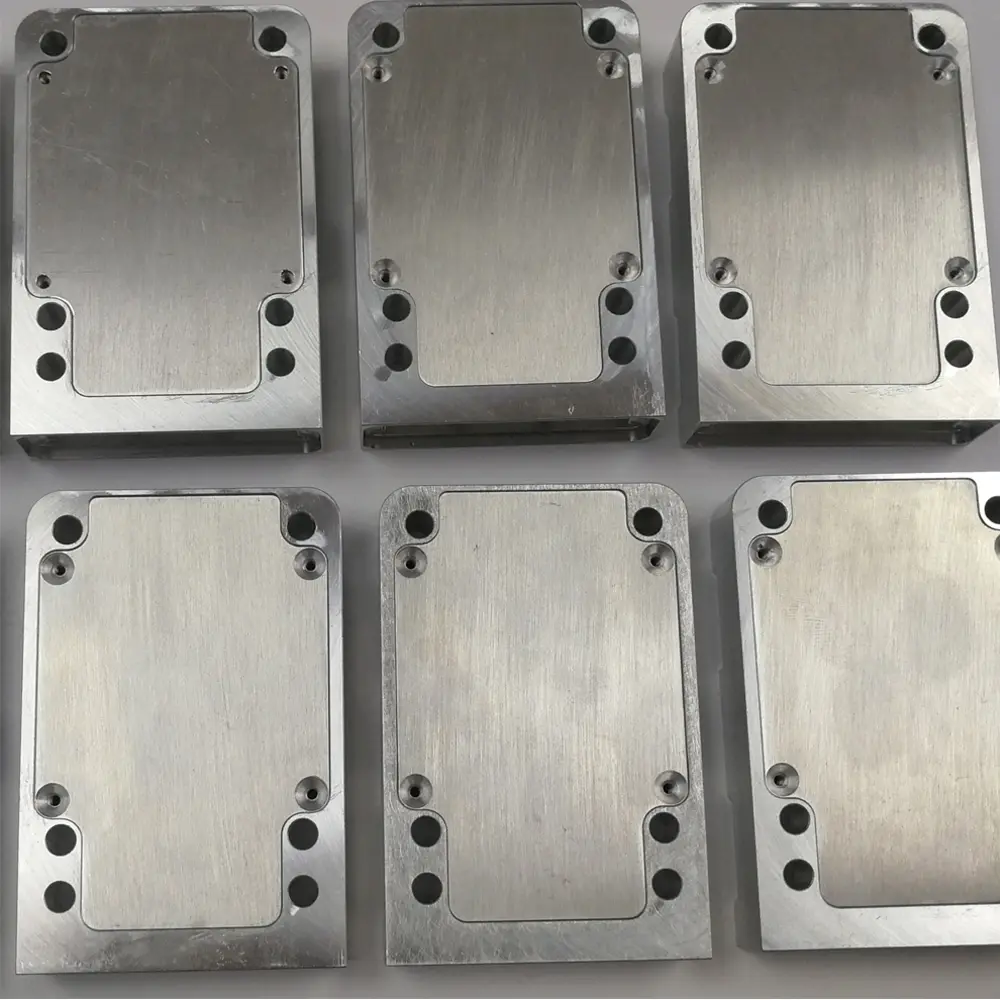
Low Volume Production with Manufacturing Process for Aluminum Housing and Lid
Aluminum VS Copper Heatsink with High & Thin Fins in Which Cutting Depth is Nearly 20 Times Bigger than Cutter Diameter
Manufacturing Services: CNC Machining, Wire EDM
Finishing Services: Polishing
Material Used: Aluminum, Copper
Prototype Type: Aluminum VS Copper Heatsink Prototype
Challenge: Machining out high and thin fins
Prototyping Quantity: 80pcs +80pcs
Lead Time: 20 days
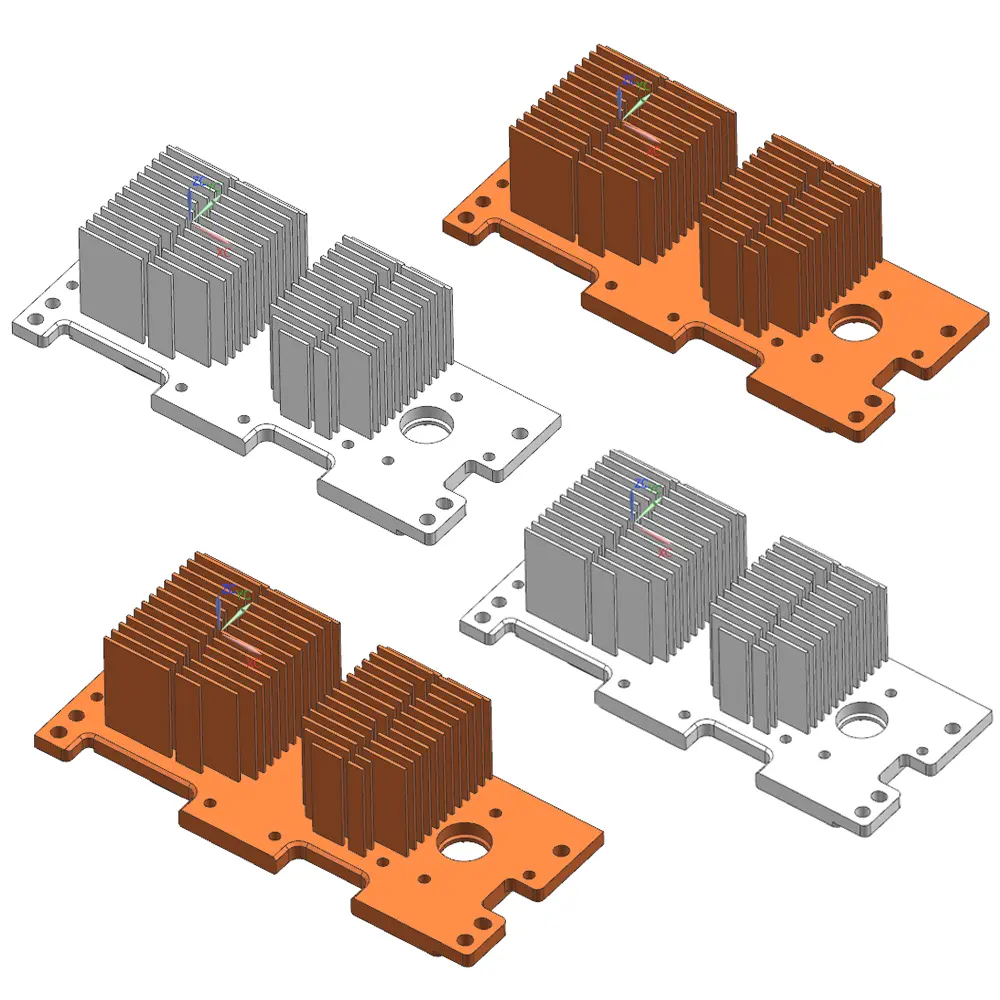
About the Aluminum VS Copper Heatsink Prototype
This aluminum VS copper heatsink prototype is from a customer who is working on heat sink test. The customer needs these heatsink samples for a comparison test. So, he placed an order with 80pcs aluminum and 80pcs copper heatsinks. Different material heat sinks are designed in same geometry. And the customer wants us to use the same process to keep the similar tolerance for all the samples. This does help to his heatsink comparison test.
These aluminum VS copper heat sink samples have very high fins which are nearly 15 times bigger than end mill diameter. Besides this, the fin gaps are not in the same, some are wide but others are narrow. The heatsinks are called out many tight tolerances for fin dimensions since these fins are related to thermal radiating test. Any deviation from geometry would affect thermal radiating result. Additionally, some regions of these heatsink have to be polished since it will assembly with other parts and these surfaces are designed for good thermal conductance.
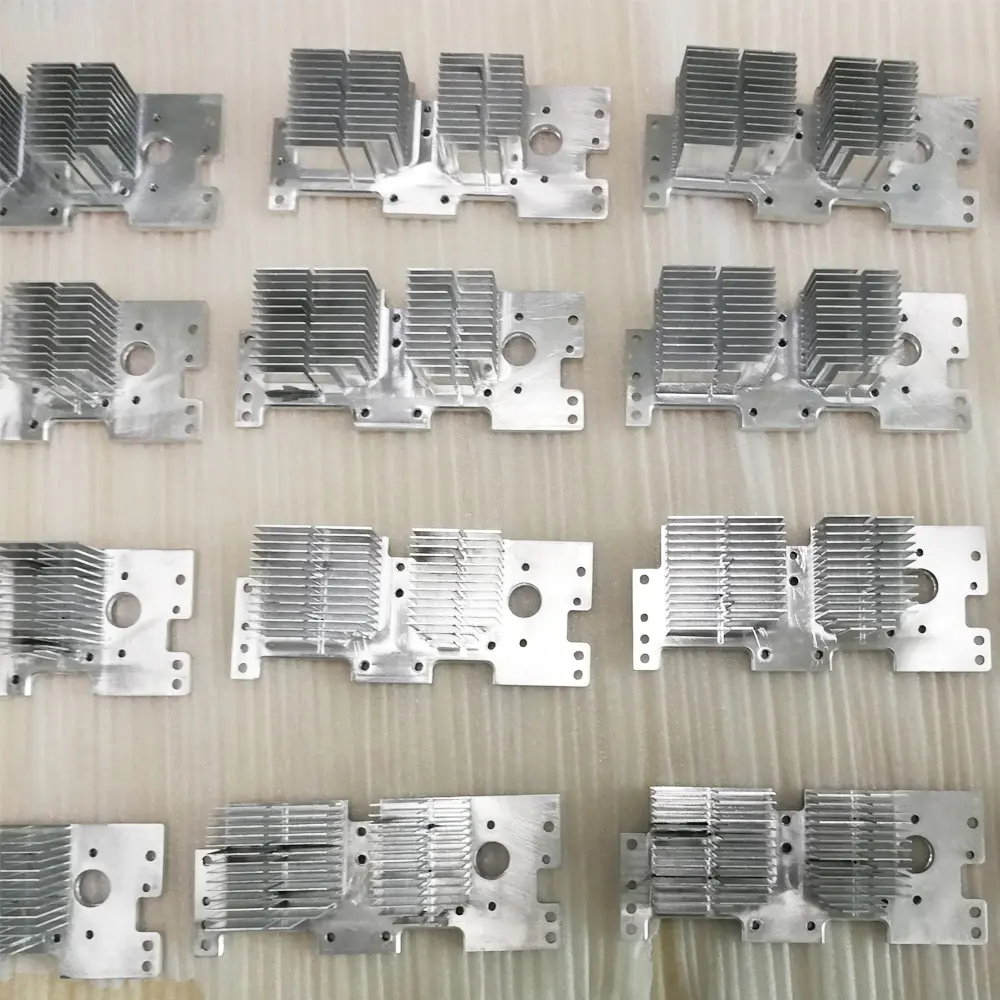
Challenges in Heatsink Prototype
For these aluminum VS copper heatsink samples, from our experience, if the cutting depth is 10 times than end mill diameter, the cutter will be easily broken. However, the customers need lower cost and cannot accept wire EDM due to its high cost. So, we tried many times with optimizing machining parameters for these heatsink samples including cutting path, cutting depth, speed and even coolant.
Finally, we got the proper cutting parameters for cutting aluminum heat sink. This CNC parameters configs successfully instead of wire EDM. However, the copper heatsinks failed even we tried to calibrate and adjust manufacturing parameter for many times. At last, we have to adopt wire EDM for copper heatsinks. After this aluminum VS copper heatsink project, we tried another process which is sawing the fins of heat sink and it can saw depth 20 times than fin gap width. This new process will be used for our coming project which has high and thin fins. For more cases, you can review on our Facebook page or YouTube channel.
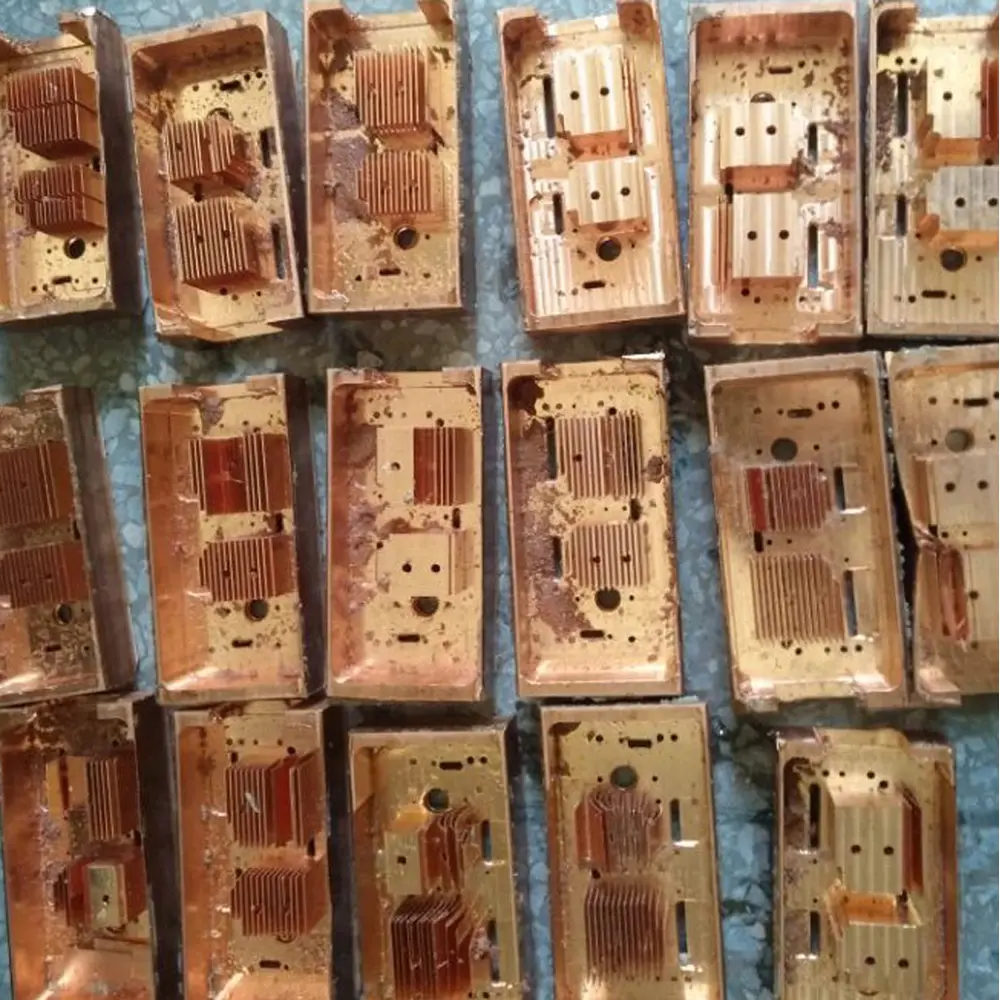