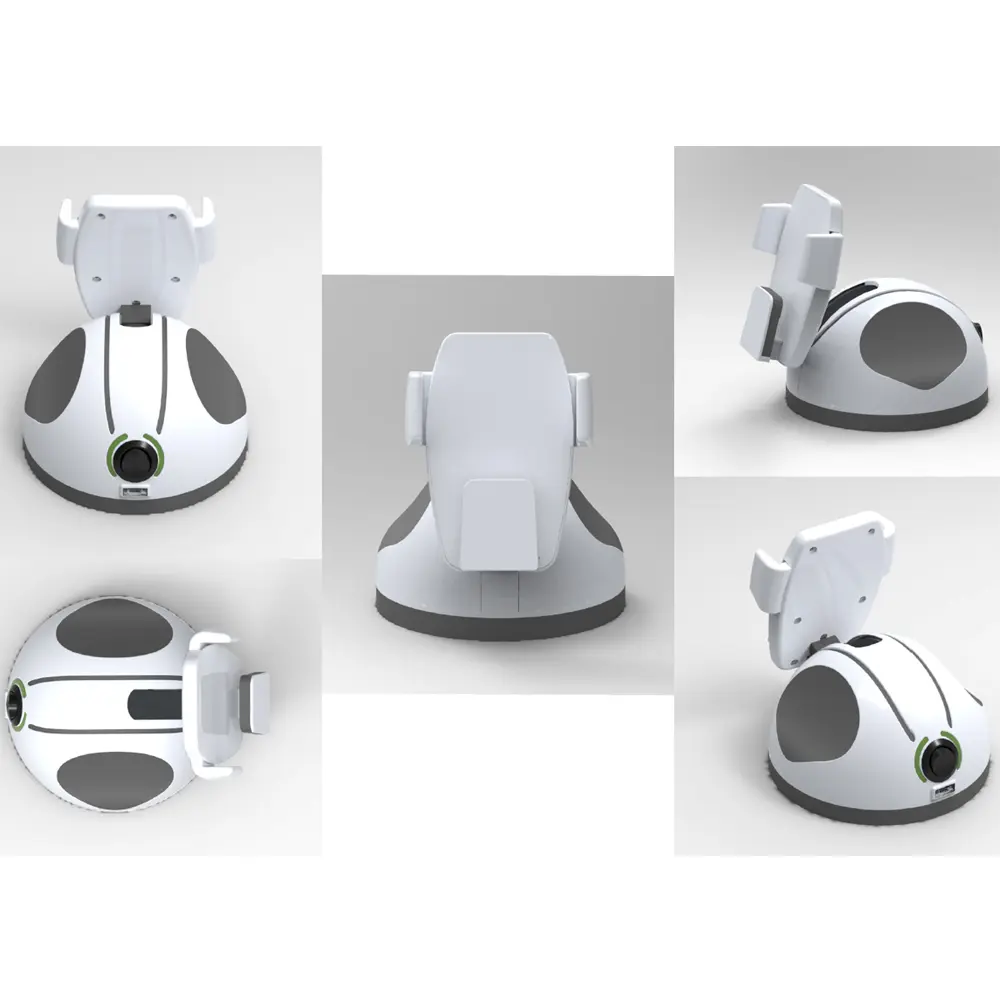
A 360 Degree Smartphone Video Chat Device Hardware Prototyping
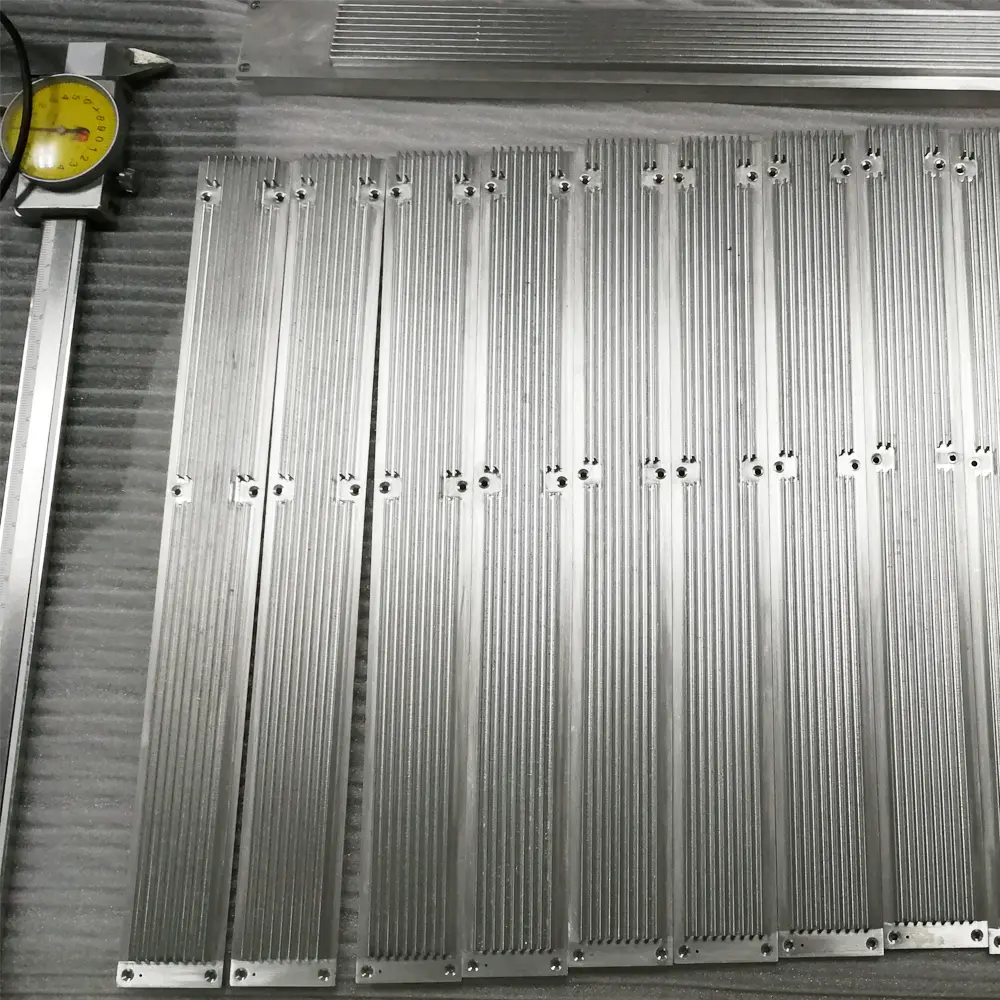
Anodized Aluminum Enclosure with Specified Region Keeping Free from Anodization
A bus Model Prototype for Wind Tunnel Test in Laboratory with High Stability and Precision
Manufacturing Services: CNC Machining, Vacuum casting, Sheet metal, Copper Nuts Insert, Gluing, Assembly.
Finishing Services: Manual Polishing, Painting
Material Used: ABS, Copper, Stainless Steel, Silicone
Prototype Type: Bus model prototype
Challenge: Improving overall strength
Prototyping Quantity: 1 set
Lead Time: 20 days
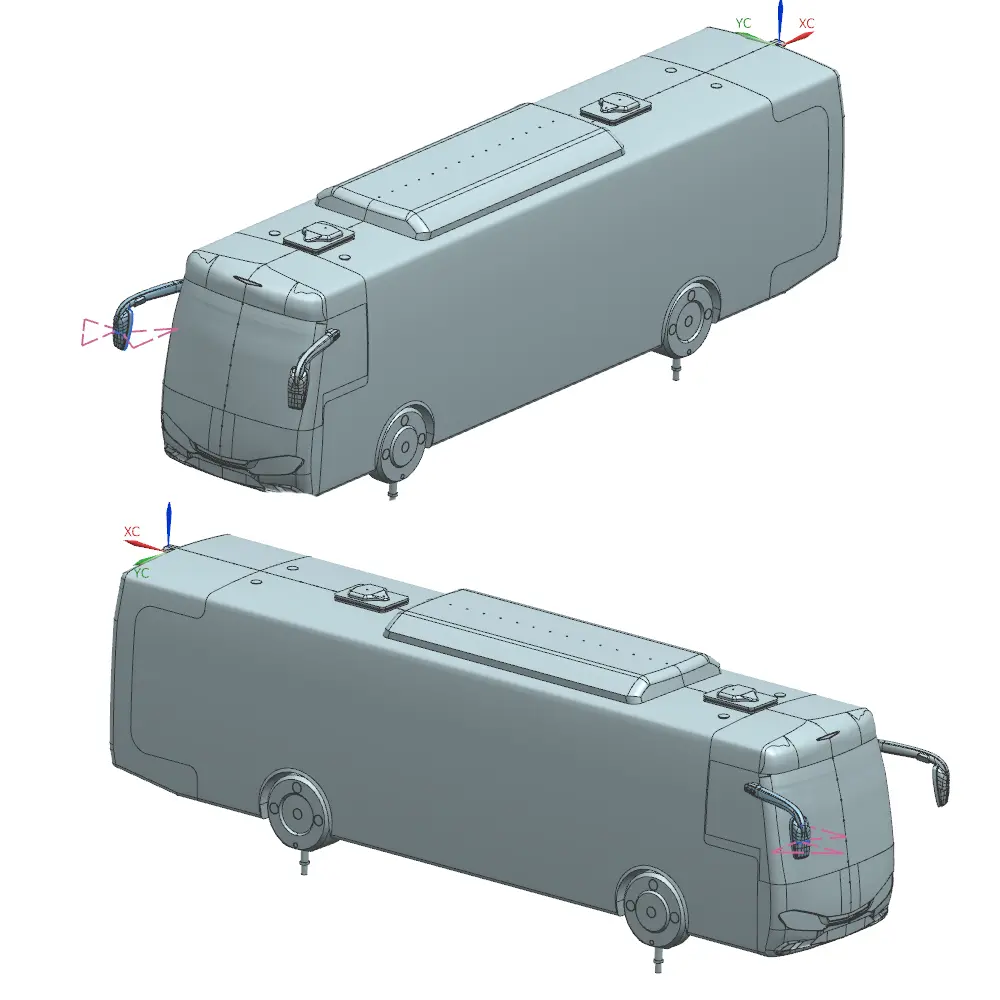
About the Bus Model Prototype
This bus model project is from a University National Laboratory. The customer needs to get some experimental data by testing the bus model in wind tunnel. The customer provided us the scanned model of bus profile and we need to design all the internal structure and connections. And the designed structure must be stable and reliable since the customer need this bus model for many times tests in different wind tunnel parameters, including high wind speed of 50m/s. The customer provided requirements below:
- The whole model must be stable and reliable.
- The outer profiles must match the scanned model in high precision.
- The Model must support easy assembly and dis-assembly.
- The front face of the model must be replaceable for alternative tests.
- The total weight of the bus model must be within 100KG.
- The wind airflow pipes must be unblocked and be flexible for detector.
- The dimension tolerance of wheelbase and track must be within +/-0.20mm.
- The appearance should be in good-looking with silver painting.
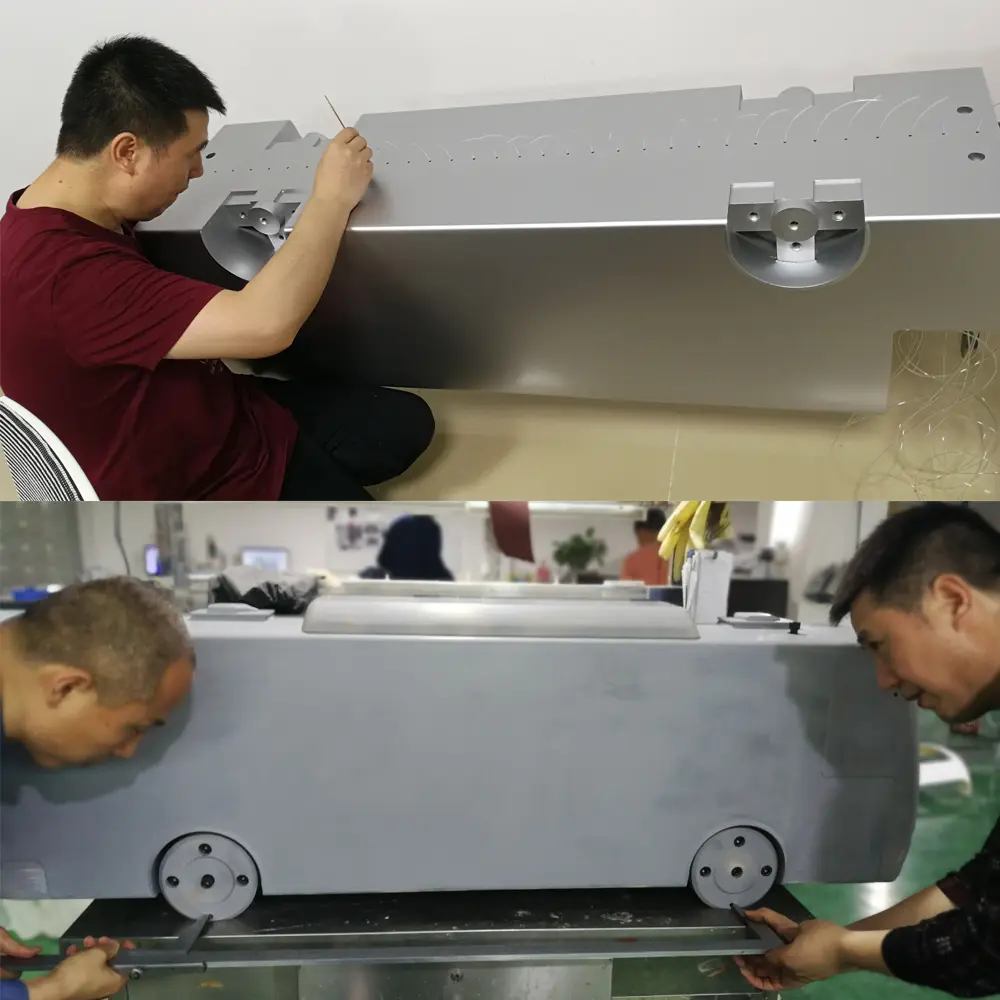
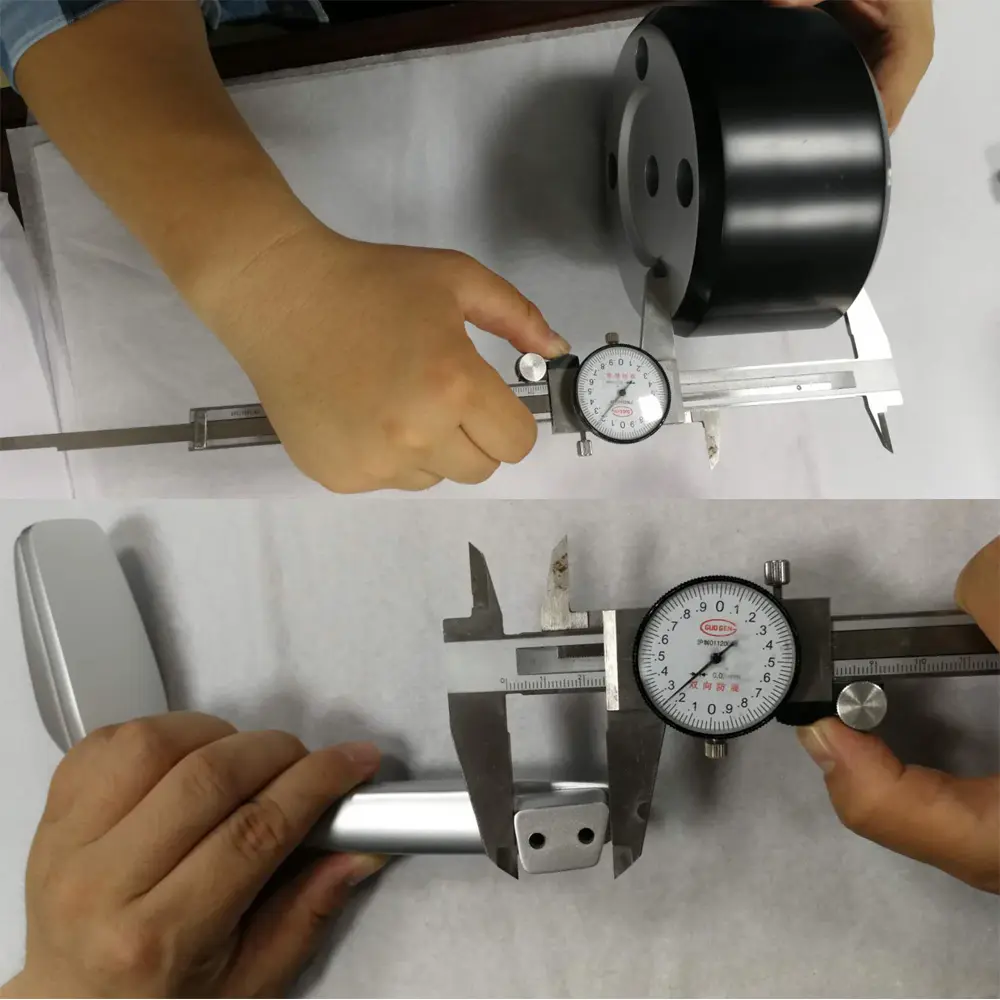
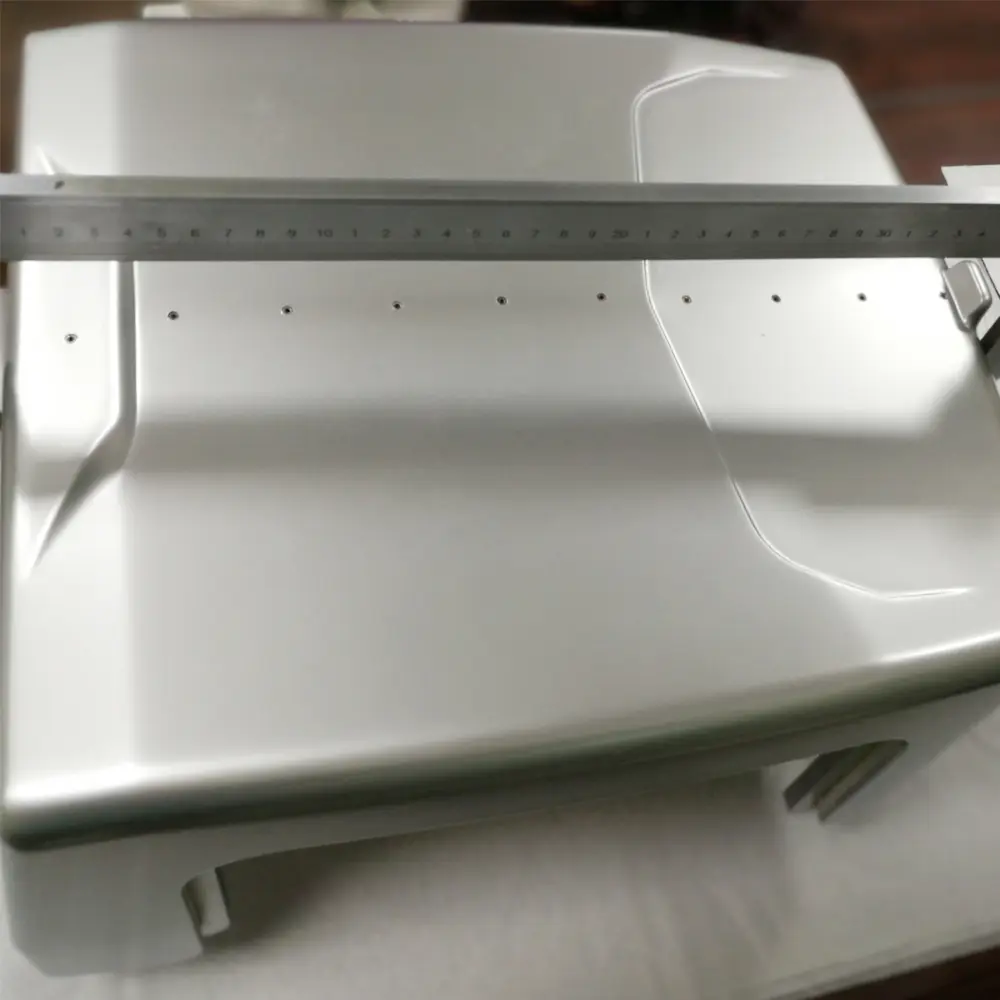
Challenges in Bus Model Prototype
For bus model prototype, the internal design and manufacturing are all the challenge for us since the customer uses it in wind tunnel test with wind speed of 50m/s. We have to design a very stable and reliable structure inside. Otherwise, some small parts such as back mirror, surface plugs have high possibility to drop during high speed wind tunnel testing. OrideTech designed many strong self-lock features inside and also design many ribs for strengthening the support from inside. Even so, we still have some screws design which must be locked from inside and leave recess from outside for this bus model prototype. Due to abnormal wind flow generated from outside recess, we designed many silicone plugs to fill the recess and keep flush with the outside surface.
The dimensions challenge is to control the overall length, width and height into +/-0.20mm. We adopted many compensations during CNC machining and polishing the sections during assembly. Finally, after many rounds of manufacturing, correcting and inspecting, we got all the dimensions into these specifications. For strength, due to the internal design, we got the model tested for standing 500kg force. For more cases, you can review on our Facebook page or YouTube channel.
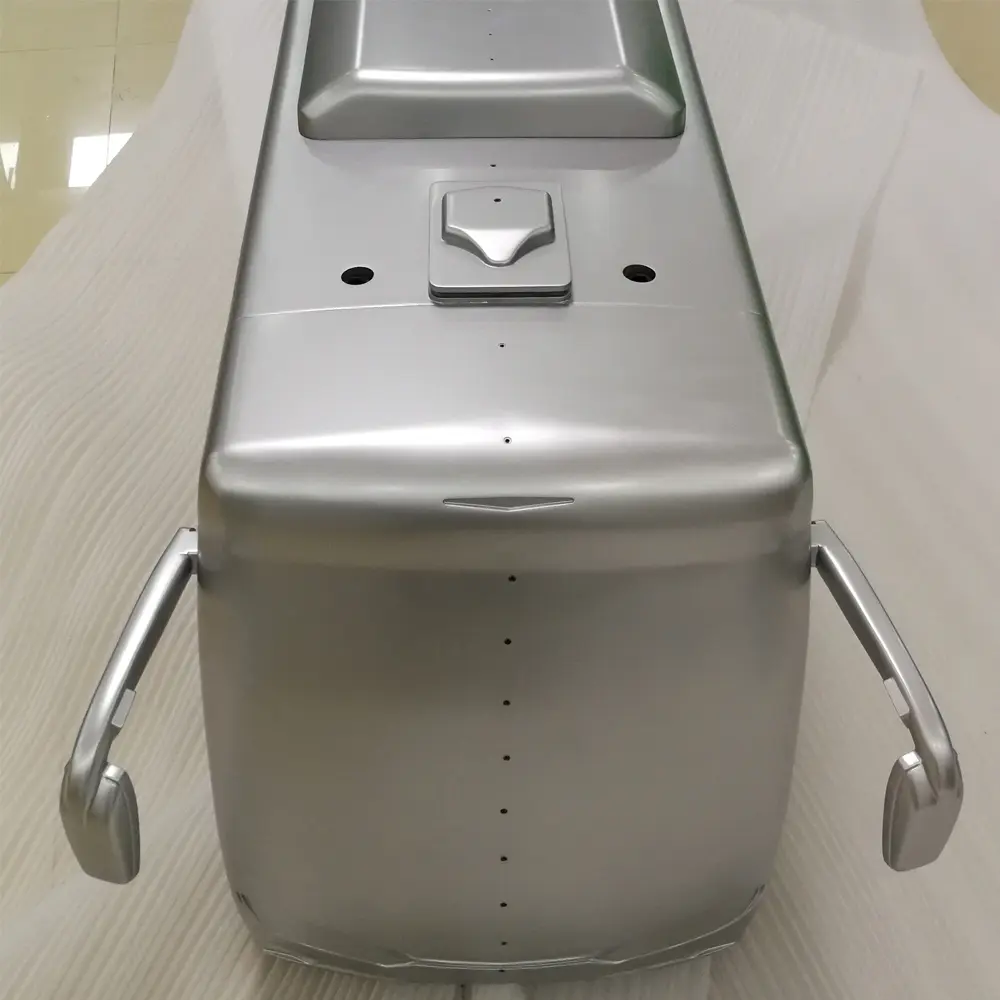