What is Sheet Metal Fabrication?
Sheet metal fabrication is a manufacturing process that involves cutting, bending, shaping, riveting and assembling metal sheets to create a final product. Sheet metal fabrication is commonly used in the production of various products, including enclosures, cabinets, brackets, and assemblies. The process involves using a variety of tools and techniques, such as CNC machines, shearing, punching, and laser welding, laser cutting to make the metal sheets into the designed shape and size.
OrideTech’s sheet metal fabrication processes are available for machining parts from prototype and low-volume production into good quality with lower price for customers. For more details and videos, you can review on our Facebook page or YouTube channel.
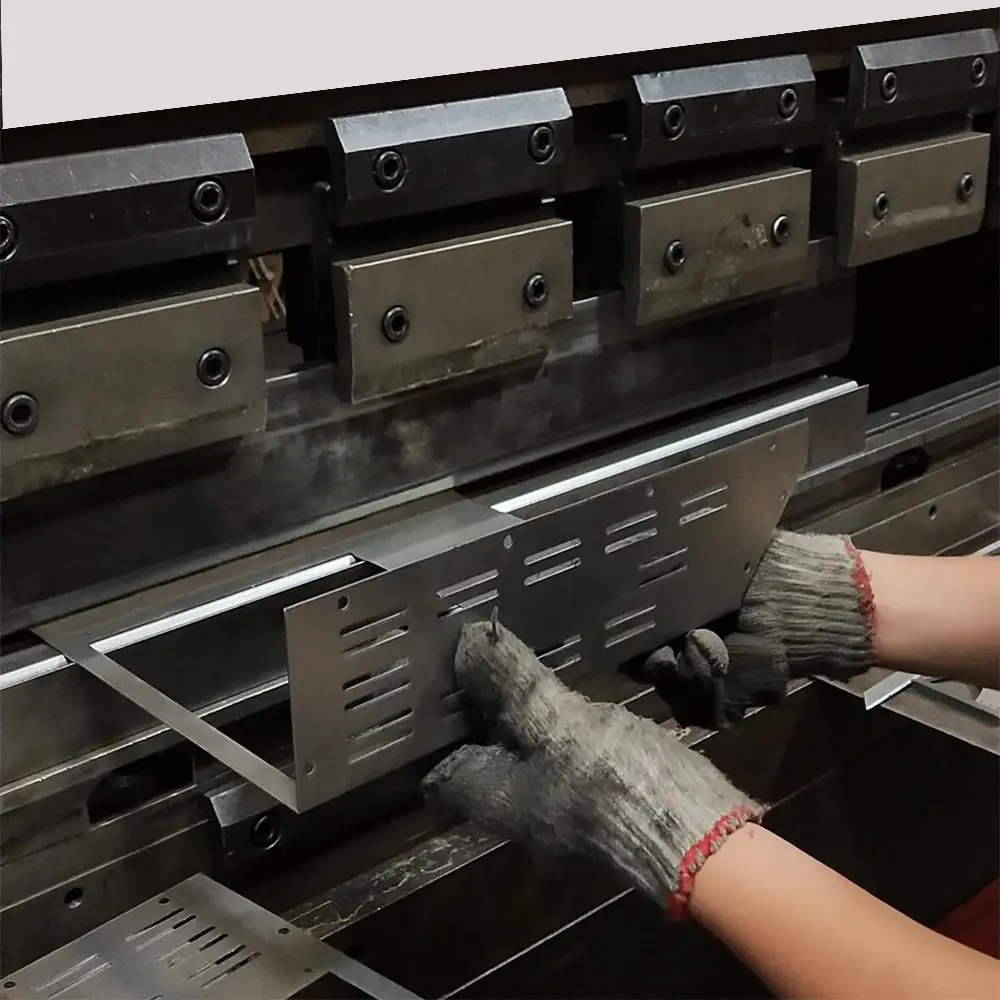
Sheet Metal Material Options
Sheet metal fabrication can work with a variety of materials. It works with stainless steel, aluminum, brass, copper, and carbon steel. The choice of material depends on the specific requirements of the product, such as strength, durability, and corrosion resistance. The thickness of the sheet metal can also vary ranging from thin films to thick plates. OrideTech stocked some common use material below for support customer’s urgent projects in prototype and low-volume production.
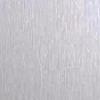
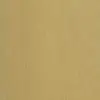

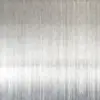
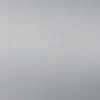
Advantages of Sheet Metal Process
OrideTech set sheet metal fabrication for making samples for prototype and low-volume production since it has many advantages below
1. One of the main advantages of sheet metal machining is its versatility and flexibility. The process allows for the creation of complex shapes and designs, as well as the ability to produce both large and small quantities of parts.
2. Sheet metal fabrication is also relatively fast and cost-effective, especially when compared to other manufacturing processes such as casting or forging.
3. Sheet metal process is highly accurate and precise, which is essential for parts from many industries and applications.
4. The parts after sheet metal process can be applied with most finishing like plating, anodize, marking and powder coating.
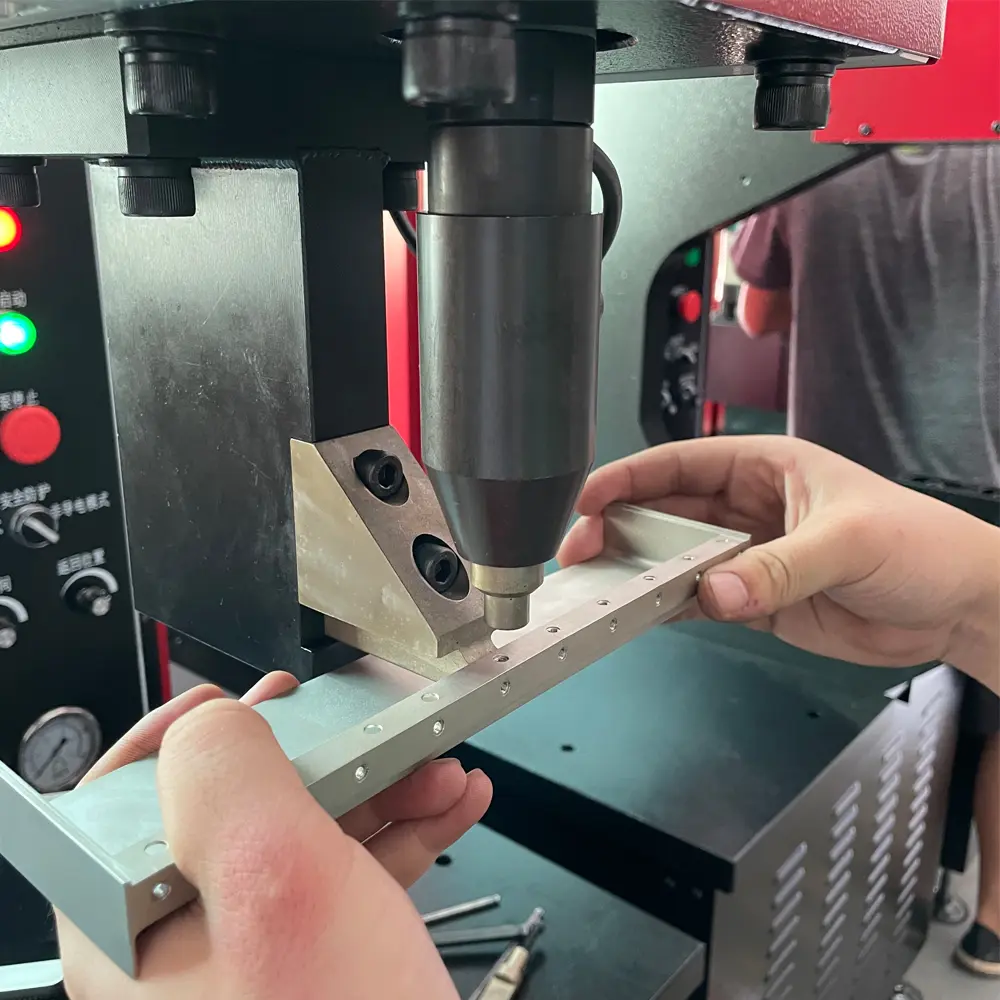
How Does Sheet Metal Process Work?
Sheet metal fabrication typically involves several steps, including cutting, bending, punching, riveting, welding and assembling. The process begins with a flat sheet of metal that is cut into the desired shape and size using specialized cutting tools such as shears or laser cutters. The metal sheet is then bent into the desired shape using a press brake in bending equipment. Some features such as holes, chamfers, recesses and slots can be punched or drilled into the metal sheet. Finally, the individual parts are assembled and welded together to create the final product. OrideTech uses these processes for sheet metal parts in customer’s project. Both prototype and low-volume production, from serval parts to small quantity parts, these sheet metal fabrication processes can always be useful.
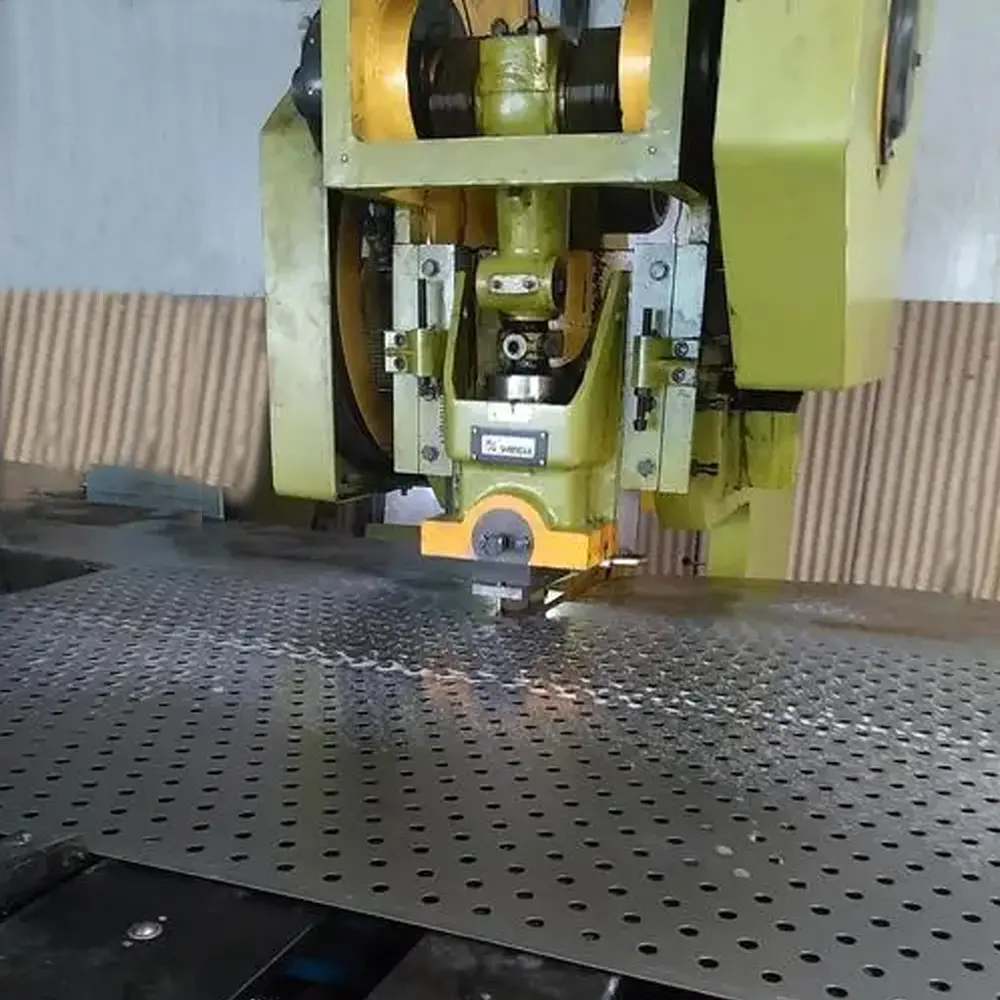
Why Choose Oride for Sheet Metal Parts?
OrideTech has been providing high quality sheet metal products for more than 8 years. It has full processes including cutting, bending, punching, riveting, laser welding and assembling for your parts from both prototyping to low-volume production. Besides, it also can provide you service below:
- Top priority samples can be finished within 24 hours to support your urgent project.
- Manufacturability and cost-saving proposals be provided before your samples kick off.
- Cost free pre-assembly service be provided before shipping to make sure all the parts work well.
- Full processes including finishing like plating, anodize and powder coating be provided to save your product developing time.
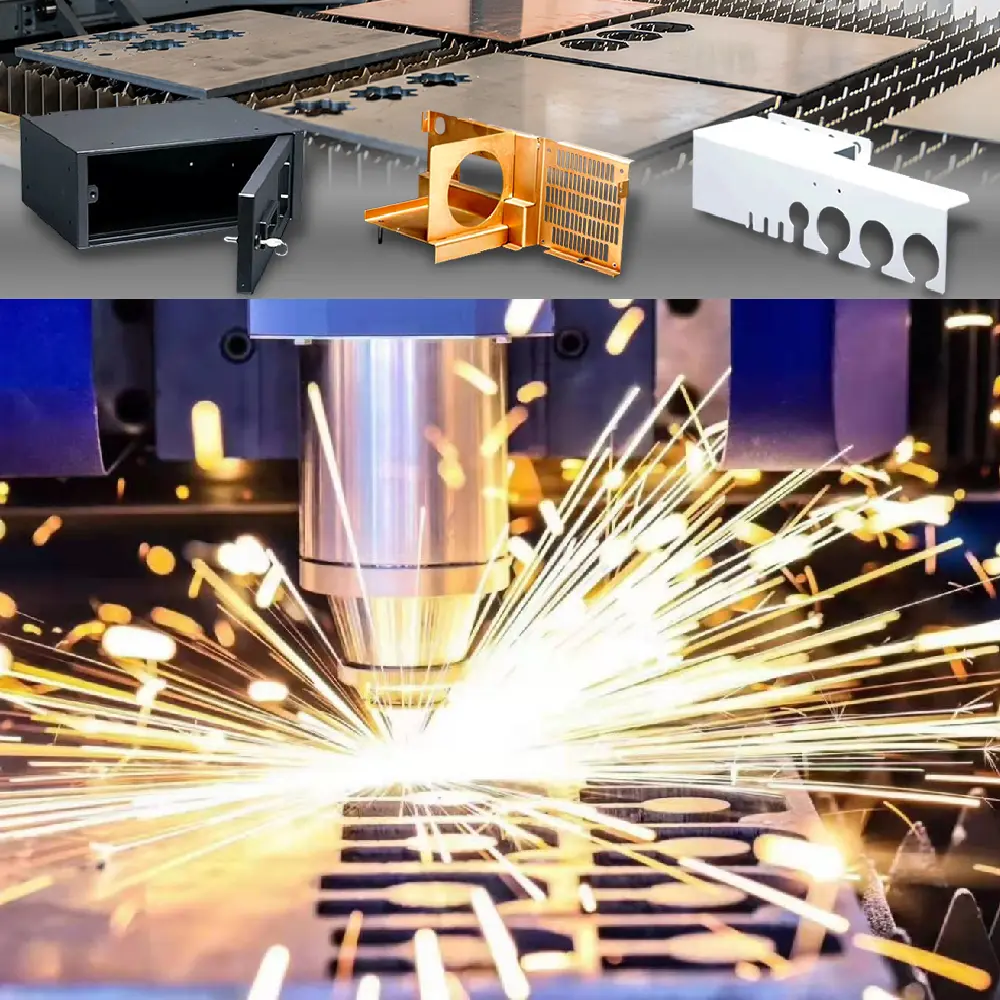