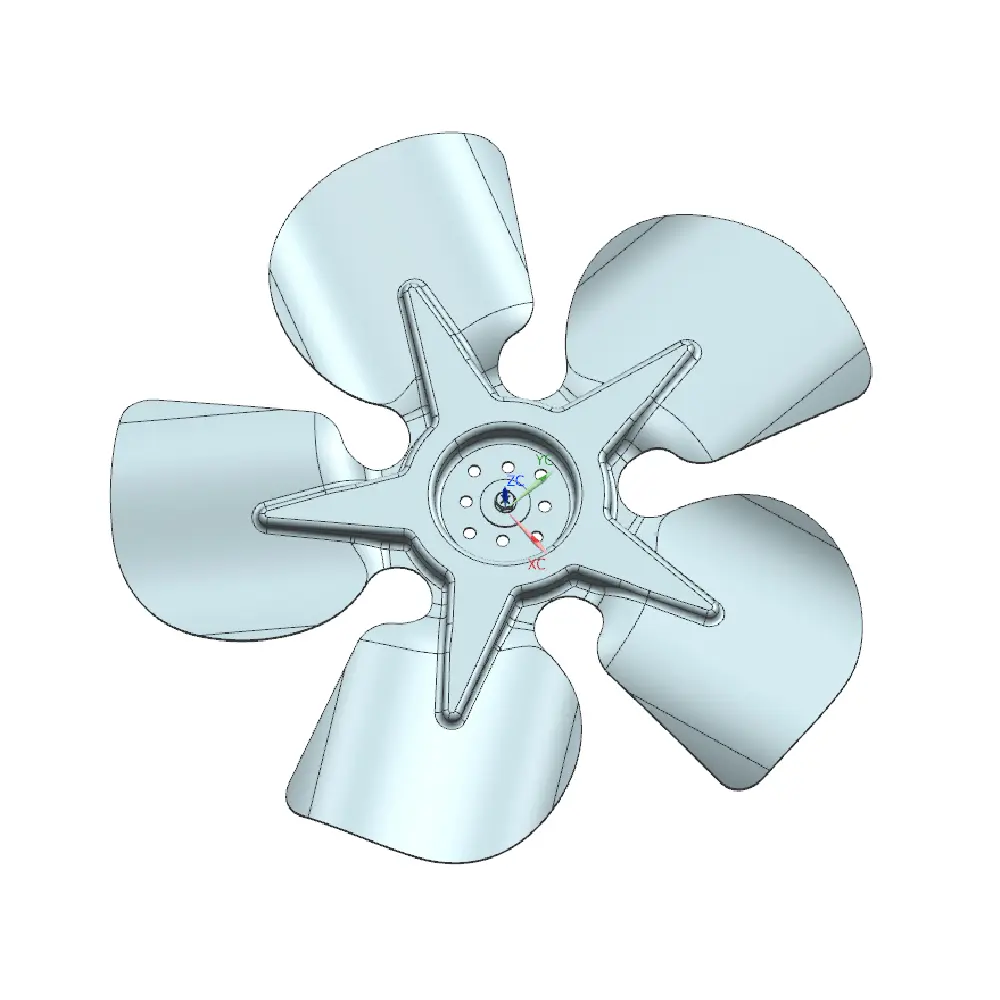
How to Make a Design Change Request During Prototyping Sample Fabricating?
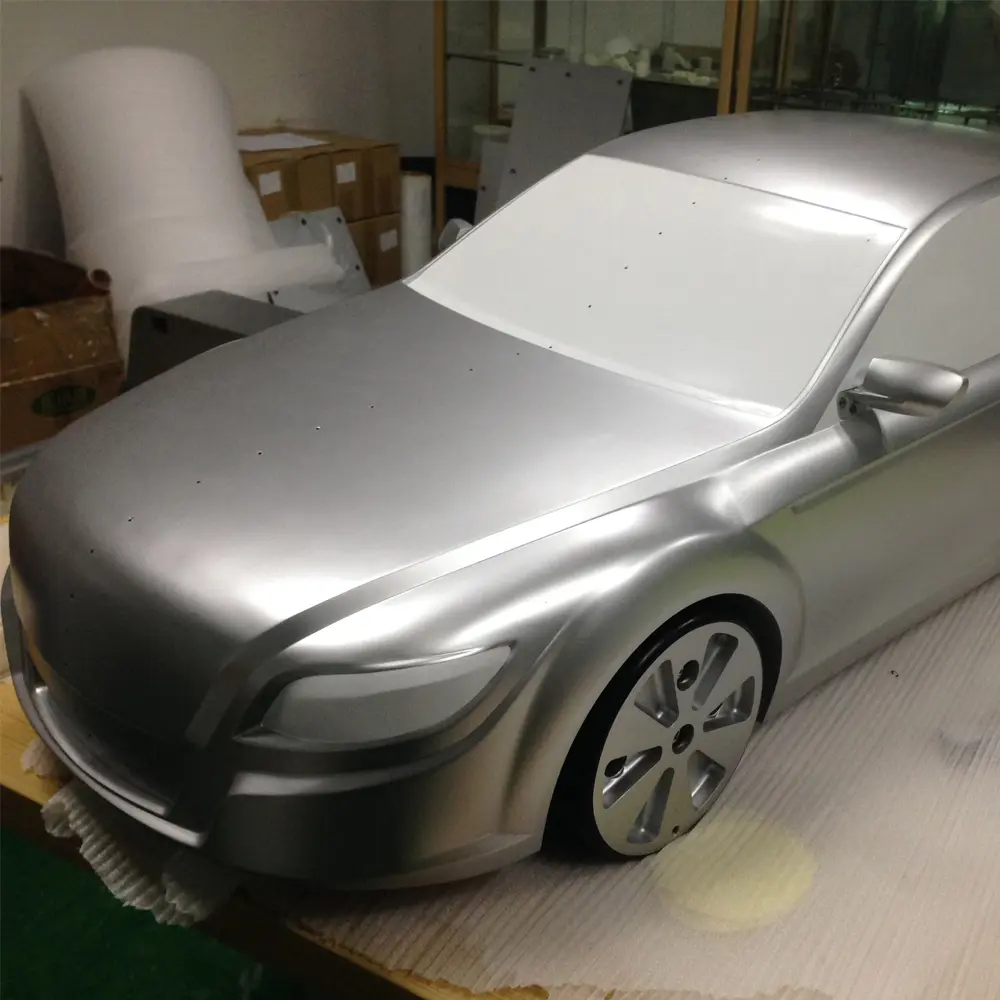
What Manual Operation Processes Does Oride Provide to Make Samples in Good Look
What Inspection and Measurement Service can OrideTech Provide?
As we know, inspection and measurement are very important to rapid prototyping samples. And the customers use inspection and measurement data to evaluate the samples quality. And also, some inspection and measurement data are related to the assembly and function. So, OrideTech provides inspection and measurement service to all customers. Most time, the customers need these data for evaluating samples. Besides the current inspection and measurement equipment, OrideTech is countinuing inputing more resources and equipment for providing better inspection and measurement service.
1. Calipers Dimensions Measurement
Caliper is a measuring tool commonly used in prototyping. It can accurately measure the distance between two opposite sides of an object. This allows designers and engineers to take precise measurements of components. Caliper can measure the thickness, the diameters and the distance between two points. Also, the caliper is easy to use for both designers and engineers. OrideTech has many different calipers which can support measuring dimensions from 0.01mm to 1000.00mm. OrideTech also have a very detailed standard calibrating procedures to ensure all the calipers are working in good situation.
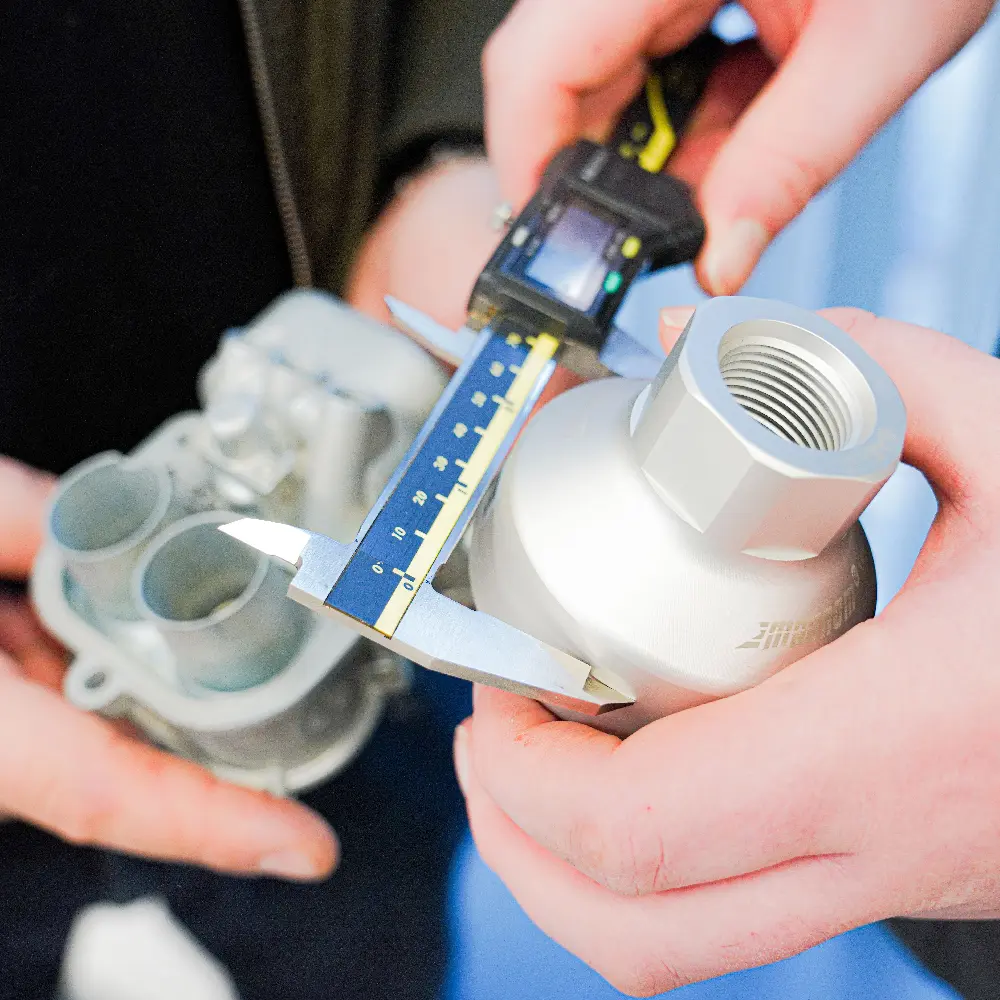
2. Roughness Measurement
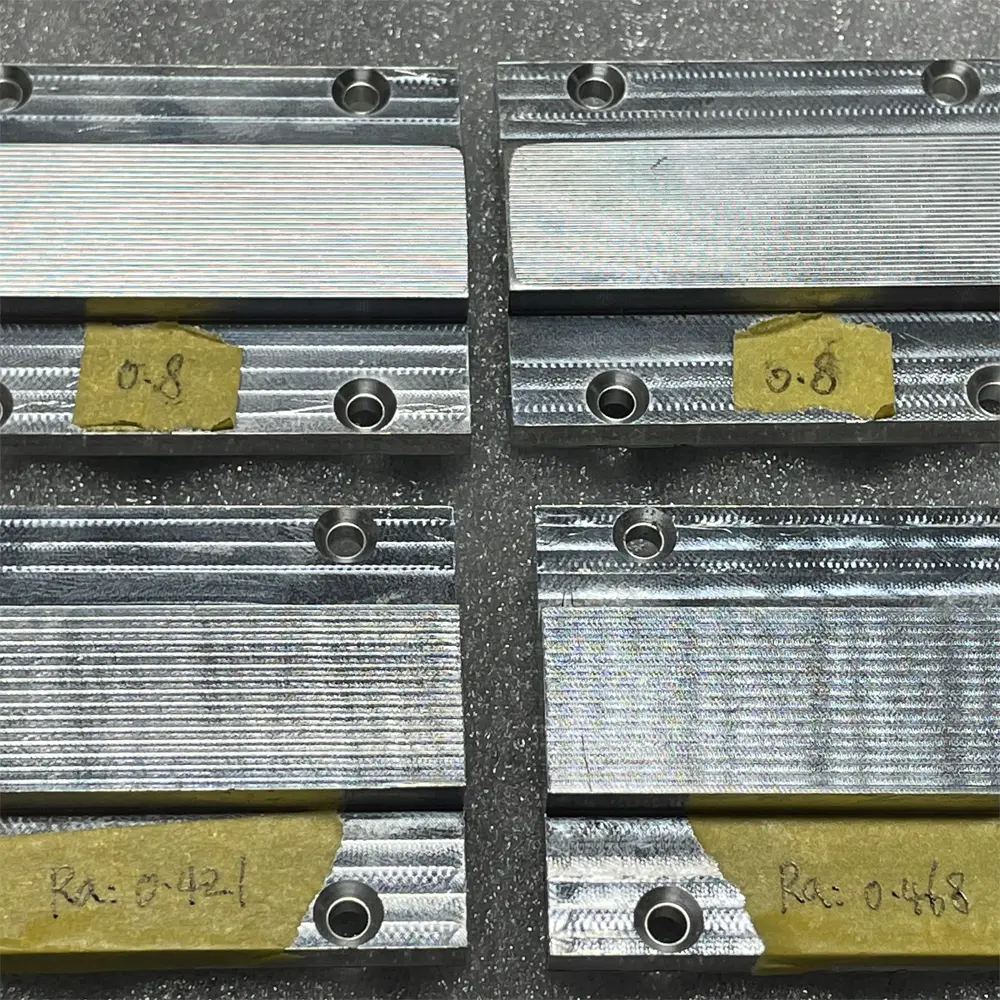
In prototyping inspection and measurement, roughness measuring is used to evaluate the surface texture. It is an important consideration in many applications because surface roughness affects the performance and functionality of a part. Roughness measuring involves surface roughness testers to measure parameters such as Ra (roughness average) or Rz (average maximum height of the surface irregularities) of the surface. These measurements can help designers and engineers to determine the appropriate finishing process for a part. It also ensures that the part meets the required specifications. Sometimes, the customer needs to do samples in different roughness to compare which is more suit to his product. All these inspection and measurement are available in OrideTech.
3. Flatness Measurement
In prototyping inspection and measurement, flatness measuring is used to evaluate the flatness of a surface or a part. In prototyping, it is important to ensure that the surfaces of parts or components are flat. The flatness has to be in tolerances to ensure proper fit and function. The flatness measurement data are typically reported in terms of the deviation from the perfect plane in microns or other units of measurement. Flatness measuring is an important aspect of quality control in prototyping. It can ensure that parts and components meet the required specifications. For some heatsink products, the back plates are always designed to be heat conduction. So, the flatness becomes much more important.
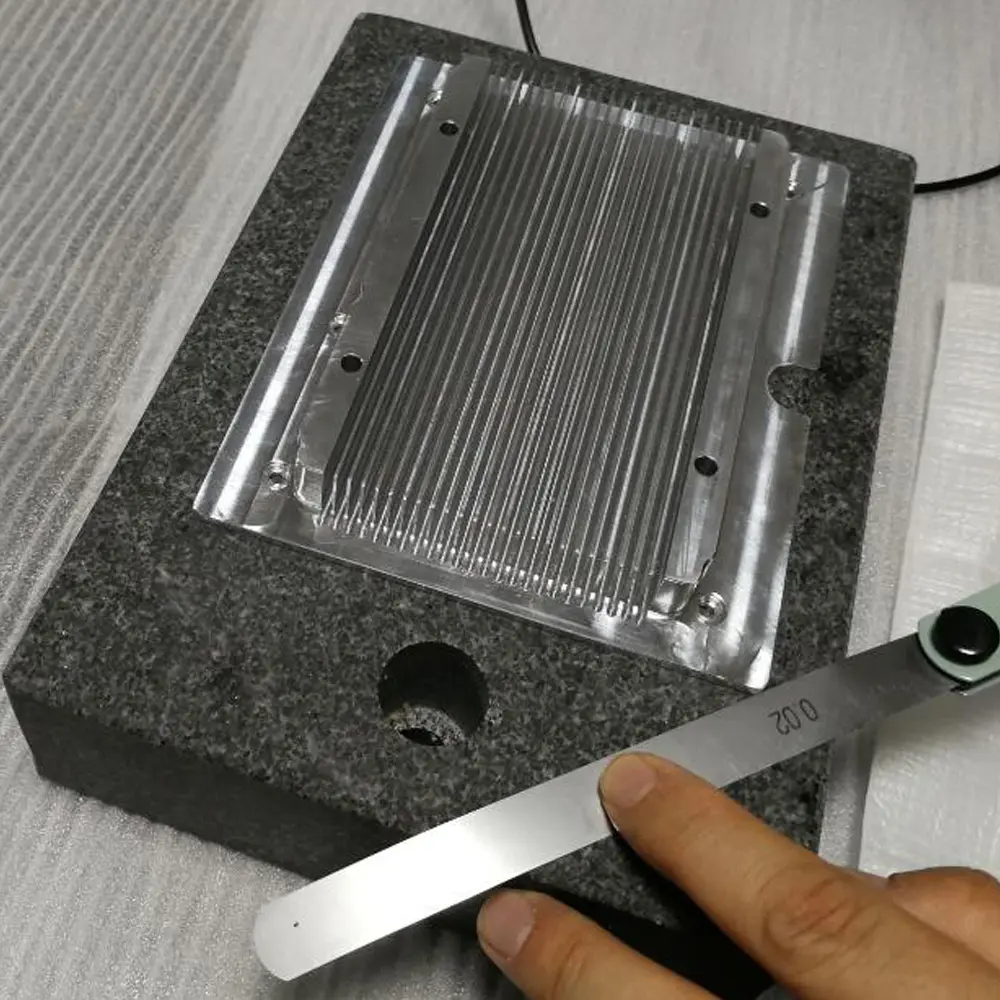
4. Pull/Push Force Test
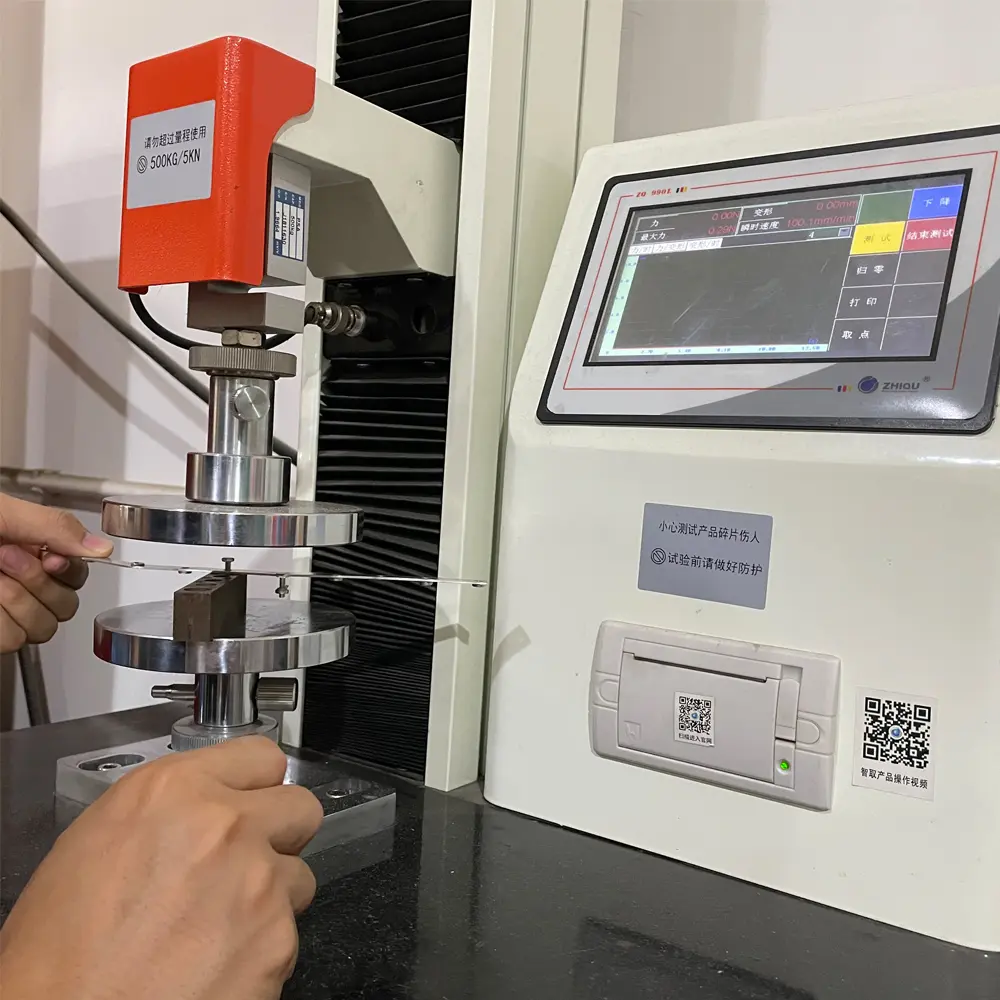
Pull/push force measuring is a type of measurement used in prototyping inspection and measurement. They can determine the amount of force required to pull or push a part in certain direction. This type of measurement is important in many applications, such as testing the strength and durability of mechanical parts, choosing a proper screw to small parts. The pull/push force measuring is an important aspect of quality control in prototyping. This data tells us that if the parts and components meet the required specifications for strength and durability. In some case, customers need pull/push force data to determine which design they need, tapping threads, helicon screws design or screws?
5. Location Dimension Measurement
Location dimension measuring is a type of dimensional measurement used in prototyping inspection and measurement to ensure that parts or components are located in the correct position relative to other parts or components. This type of measurement is important for ensuring proper fit and function of the final product. Location dimension measuring can be performed using a variety of tools and techniques. Oridetech, for now, are using optical comparators (OMM) to measure the location dimensions.
6. Screw Toque Force Test
Screw torque force measuring in prototyping inspection and measurement refers to the process of measuring the amount of torque or rotational force. This is important in prototyping because it ensures that screws are tightened to the correct level. It can affect the performance and reliability of the final product. Inaccurate torque force can cause screws to loosen or break, leading to potential safety hazards or product failure. Therefore, it is important to measure screw torque force during prototyping to ensure that the final product meets the required specifications and standards. For more blogs, you can review on our Facebook page or YouTube channel.
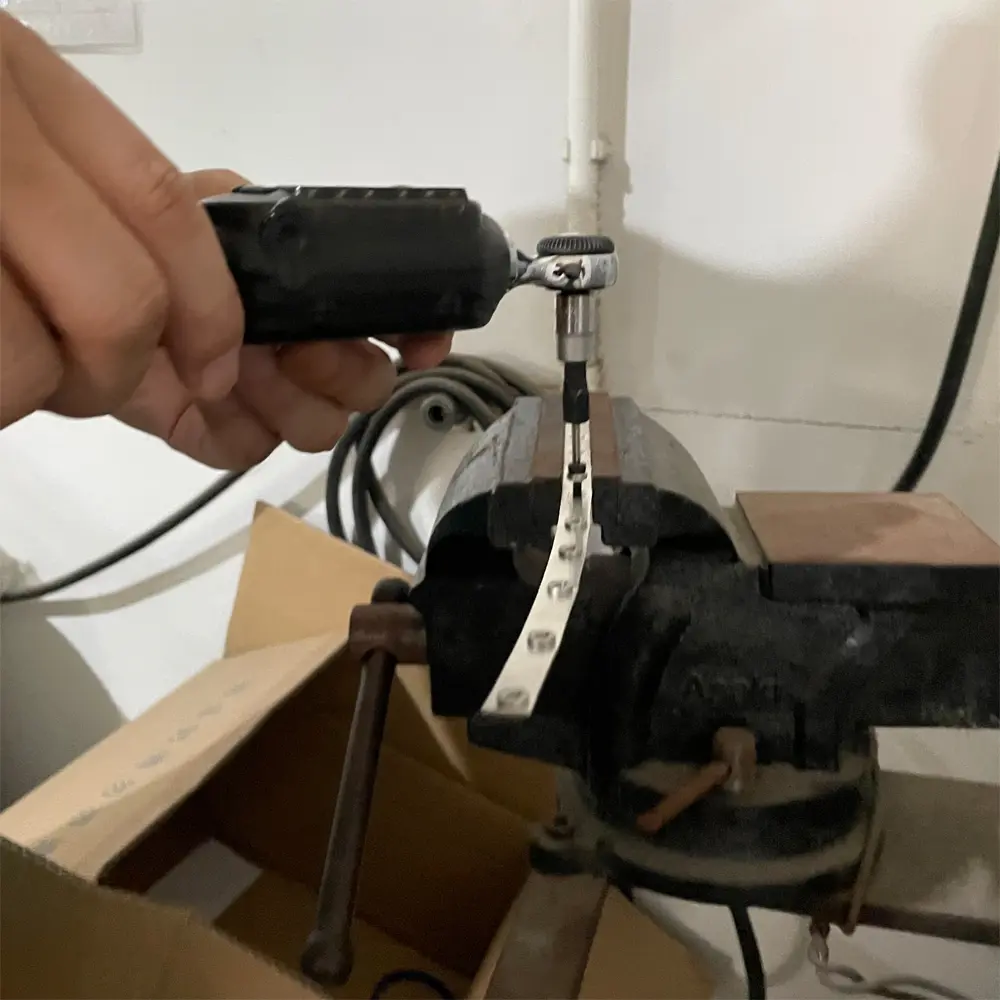